Thomson ReutersA Toyota logo is seen on a car displayed on media day at the Paris Mondial de l’Automobile
TOKYO (Reuters) – Toyota Motor’s close ties to its “keiretsu” – or family of affiliates and suppliers – have helped it become the world’s top automaker. But two major production stoppages this year highlight the risks, too.
The car maker’s reliance on Aisin Seiki Co , an affiliate, for door and engine parts forced Toyota to halt much of its production at virtually all its plants in Japan this week after an earthquake damaged Aisin plants in the south.
The stoppage follows another week-long production halt in February after a fire at another affiliate, Aichi Steel and could initially cost Toyota up to 90,000 vehicles and 30 billion yen ($275 million) in profit, by some estimates.
Toyota says it will restart production at most of its assembly plants in Japan next week.
Nonetheless, the two incidents at the two affiliates illustrate the delicate balance for manufacturers like Toyota to disaster-proof the supply chain – a crucial part of the ‘Just in Time’ production system it pioneered over half a century ago to improve efficiency and reduce wastage.
“Just in Time works when everything’s running smoothly,” said CLSA analyst Christopher Richter. “But if you balance the cost (of holding more inventory) for however long you have between these disruptive events, it would probably be worth sticking with the system.”
And that’s what Toyota is doing.
“The Just in Time system is to ensure we receive supply as we need and only in amounts required at the time. We have no plans to change this policy,” a company spokesman told Reuters.
“It takes time to procure the 30,000 parts we need to produce each vehicle. Bringing all these parts together is a massive process, so we’re always looking to strengthen our supply chain, but we’re not considering changing the inventories we hold (because of the recent earthquake).”
RIPPLE EFFECT
Toyota says it needs to produce at least 3 million vehicles domestically each year to keep its plants, and those of its suppliers, operating efficiently, while also making its product development arm competitive.
“If this base were to crumble because we shifted too many operations overseas, we would lose our domestic manufacturing expertise,” the Toyota spokesman said.
Toyota has, though, pushed some of its core suppliers to find more customers so they don’t over-rely on the ‘keiretsu’ at times of disruption.
Around 62 percent of Aisin’s sales now go to Toyota, down from 68 percent before the devastating 2011 earthquake and tsunami. Big, non-Toyota customers now include Volkswagen , Audi , Peugeot
and Volvo.
But the sheer size of orders from Toyota – which gobbles up 90 percent of Aisin’s Japan-made door check straps – means any disruption at just one supplier can have a disproportionate ripple-on effect across the automaker’s production lines.
‘MADE IN JAPAN’
Also, Toyota’s ‘Made-in-Japan’ ethos carries risk when disaster strikes. Investors will have noted that while Toyota shut down in Japan because of quake damage to its supply chain, rival automaker Nissan Motor remained operational.
Nissan, and third-ranked Honda Motor , make less than a fifth of their vehicles in Japan, having shifted more production overseas after 2011. Toyota produces 40 percent of its global output at home.
But for Toyota, which with its group companies employs well over 150,000 people in Japan, its status as the country’s flagship company also carries a high responsibility and can come before maximizing profits in the short term.
Nissan, and others, though, are changing tack to minimize the disruption from a seismically active domestic production base.
“We have implemented measures since 2011 so we are better equipped to deal with natural disasters,” said Masahide Amada, Nissan’s chief product specialist. “These include diversifying production capabilities and supply chains.”
Analysts said Nissan’s plant in southern Japan avoided serious impact from the recent earthquake because it sources parts both in Japan and from South Korea and China.
“Nissan sources more parts from overseas than Toyota. This gives it a longer supply chain to avoid possible disruptions,” said Koichi Sugimoto, auto analyst at Mitsubishi UFJ Morgan Stanley Securities.
Nissan declined to comment in detail on its supply chain.
(Reporting by Naomi Tajitsu, with additional reporting by Maki Shiraki and Ami Miyazaki in TOKYO and Hyunjoo Jin in SEOUL; Editing by Ian Geoghegan)
Read the original article on Reuters. Copyright 2016. Follow Reuters on Twitter.
More from Reuters:
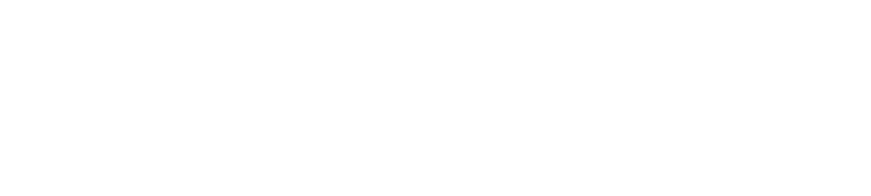