
When I bought my 2000 Jeep Cherokee for $500 a few years back, I thought I’d scored the deal of the century. The vehicle had just two previous owners, 80,000 miles on the engine, and what looked like a relatively rust-free body. But after a single winter, I inspected it a bit more closely and realized that I had been mistaken: The body wasn’t even remotely rust-free. It had an enormous hole in a critical part of the unibody. Here’s how I fixed it.
Ever since last summer, I’ve been on a quest to sell off some of my vehicles as I make a few life-recalibrations. I’ve already gotten rid of a Willys, a POStal Jeep (RIP), a Jeep Grand Wagoneer, a totaled Kia, and a Land Rover that I’d been storing. Plus, I got rid of 1,800 pounds worth of metal spare parts.
I’d like to say my house looks like a ghost town these days, but the reality is that there are still a shit-ton of cars here, somehow. Honestly, it makes no sense.
Anyway, I’m looking to reduce the count from “shit ton” to perhaps “shit kip” (a “kip” is a half a ton, I just learned). First on the chopping block is this 2000 Jeep Cherokee, though with a giant structure-compromising rust hole, it’s basically worthless. It’s possible that someone would pay $1,000, but that someone would have to be absolutely smitten by this Jeep. Possibly even drunk.
As I’m keen to maximize profit, and more importantly, keep one of the greatest Jeeps of all time out of the great junkyard in the sky, I set out to fix the Jeep’s unfortunate aperture.

As a refresher, the photo above shows how the rust spot looked in the fall. Clearly, the metal had begun flaking. After a bit of prodding with a flathead screwdriver, a hole emerged:

A huge hole:

Since I needed to find some strong metal to weld to, I cut out all of the rust in this area, leaving me with a gargantuan window into the innards of the Jeep’s unibody rail:

A couple of images above, you’ll see a crossmember that mounts to this location. That crossmember holds up the transmission, and is held to the Jeep’s unibody rails via two fasteners on each side of the vehicle. Both of the provisions for those fasteners (one stud and one threaded hole to receive a bolt), however, were surrounded by rust, so I had to cut them out.
I used scissors and a piece of cardboard to make a template, then I cut a piece of 1/8-inch steel into a shape that would fill the rust hole. I then held the steel in place with magnets, and welded it to the unibody rail:

I did this two more times. (I also drilled two holes into the bottom piece, then welded two bolts inside those holes to act as fasteners for the aforementioned crossmember.) Here’s the result of my admittedly-rather-messy work with my $100 Harbor Freight Welder:

The steel cost me nothing, as I had it sitting around. But as a backup, I bought this unibody stiffener for $169 to reinforce my patch, :

That stiffener goes under the main rail, and along the outside. I spent a long, long time welding it up in below-freezing weather. A Jalopnik reader actually saw the weld sparks from the road (it was nighttime). In an incredibly stereotypical David Tracy-moment , I crawled out from the $500 Jeep whose enormous rust hole I was welding shut with a $100 Harbor Freight Welder, only to chat in German with an engineer from my second country of citizenship about cars. I think he said he had a small Fiat convertible. I actually don’t remember.
Anyway, welding upside down in 20 degree weather sucks, so it’s no surprise my work isn’t the prettiest:

Seriously, some of this just looks awful—like a line of tadpoles all eating from a trough located in the seam between two pieces of steel:

This seems like a good time to use the adage: “A Grinder And Paint Makes The Welder I Ain’t.”


So now I’ve got a Jeep with a rock-solid “frame.” And I put that term in quotes because the Jeep XJ doesn’t have a traditional frame. It’s a unibody vehicle, though AMC referred to its design as “uniframe.” The Jeep’s structure consists of a ladder frame with U-shaped longitudinal rails and four crossmembers. That ladder “frame” is welded to the Jeep’s floors, making the whole thing (minus outer panels that bolt on) a single “uniframe” component.

Welding up a unibody can be a tricky process, but luckily, because the XJ’s design is so simple, this job was fairly straightforward. The engineer-side of me does feel a bit odd about reinforcing one side of the Jeep and not the other, as this could lead to additional loads on the weak side. Plus, the stiffener could cause unwanted stress concentrations.
But honestly, I don’t think that’s a huge concern. Jeep XJ owners have been using stiffeners for many years with good results, and unless this thing goes through hard-core off-roading, I don’t anticipate any issues with the unstiffened driver’s side.
Now to see how much someone will buy this thing for…
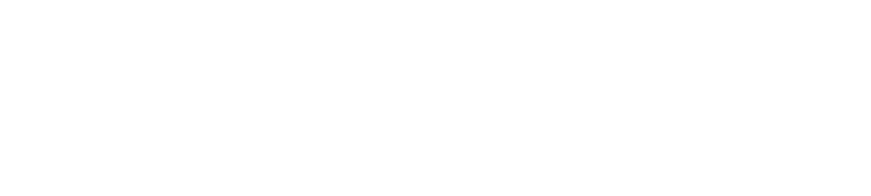