
The Koenigsegg Gemera’s name is a concatenation of the Swedish word “ge,” which means “give,” and “mera,” which means “more.” Specifically, the car is giving the world more ridiculously nerdy tech, as I learned through correspondence with the founder, Christian von Koenigsegg, and other Koenigsegg engineers. Here’s a look at the engineering behind the newly-debuted, 1,700 horsepower, four-seater Koenigsegg Gemera.
Since I don’t have access to the $1.7 million “mega car,” I can’t do a truly hadal deep dive, but that’s probably a good thing, because the Koenigsegg Gemera is a masterpiece of engineering that would take tens of thousands of words to fully explain.
Just my emails with Koenigsegg’s PR team (who forwarded me answers from Christian and the Koenigsegg engineering team)—along with information I gathered sleuthing through patents, Koenigsegg’s website, YouTube walkaround videos with Christian, and various other online sources—provided me with tremendous insight into the Gemera’s powertrain, drivetrain, body, aerodynamics, suspension, and batteries. Let’s take a look at those attributes, in that order.
Powertrain And Drivetrain

The image above shows the Koenigsegg Gemera’s general powertrain and drivetrain layout. Mounted longitudinally over the rear axle sits a 600 horsepower, 443 lb-ft three-cylinder internal combustion engine with a 400 horsepower, 369 lb-ft electric motor bolted to the back, coaxially around the engine’s crankshaft. Here’s a closer look at that motor:

Power from the internal combustion engine and inline electric “axial flux” motor (whose rotor always spins with the combustion engine’s crankshaft) goes through a long driveshaft contained inside a carbon fiber torque tube. That tube is connected to the electric motor case in the rear and to a special torque converter that Koenigsegg calls “HydraCoup” up front. From the HydraCoup, power goes to a front differential with a hydraulic clutch pack on each side (operated via a “torque vectoring distribution unit,” hydraulic pump, and hydraulic accumulator that stores pressure), yielding torque vectoring capability as the two packs apportion power between the two halfshafts that ultimately spin the front wheels.

We’ll talk more about the engine and drivetrain for the front wheels in a bit, but now let’s look at the powertrain for the rear axle. As shown above, there are two “axial flux” electric motors, each rated at 500 horsepower and 738 lb-ft of torque, and each mounted to the car’s rear aluminum subframe via rubber bushings.
Those motors each send torque through a gearbox with a parallel arrangement, meaning the output shaft—the axle—is parallel to the axis of the motor’s rotor, much like the gearboxes found in the rear drive units of all Teslas. Each of the Koenigsegg’s parallel gearboxes contain a 3.3:1 gear reduction, which is taller than what you tend to find in pure electric cars (they usually hover between 8:1 and 10:1). Despite that, the Swedish supercar manufacturer claims its car is capable of doing zero to 60 mph in only 1.9 seconds, and reaching a top speed of 250 mph. When asked about the tall gearing, Koenigsegg told me “Axial flux motors are ‘torquer’” and pointed out that the Gemera’s in particular max out at a relatively low 10,000 RPM. This is what dictated the gear ratio.
Since there’s no gearbox in the front drivetrain, the rear motors changing their direction of rotation is what allows the Gemera to drive in reverse. Here’s a look at the rear motor/gearbox I screenshotted and annotated from a Mr JWW YouTube video:

That’s pretty much the basic drivetrain layout for the front: A 400 horsepower crankshaft-mounted electric motor (which also acts as a starter, and provides regenerative braking capability) augments a 600 horsepower internal combustion engine, and sends power to the front wheels via a long driveshaft that runs through a torque tube to a torque converter, which is hooked to a 2.7:1 front differential that has two wet clutch packs (shown below) that apportion power left and right on that axle.

In the rear, torque vectoring is achieved because Koenigsegg can precisely control the two 500 HP electric motors that each power a wheel through a direct-drive gearbox with a 3.3:1 reduction. In electric-only mode, the entire front drivetrain is shut off, and only the rear motors prove thrust and regenerative braking.

The 1,700 horsepower output (that’s about 1,270 kW) of the system is less than the sum of the internal combustion engine’s max horsepower and the individual max horsepower outputs of the three electric motors. (Adding all of those up would yield 2,000 HP, not 1,700.) This is the case for two main reasons. First, power output of electric cars is largely driven by battery discharge capability, not just what the motors are capable of producing.
Second, the prime movers—the ICE and three electric machines—are geared in such a way that they yield a broad torque curve. This means torque at the wheels—which is what ultimately provides thrust for acceleration and which for this car maxes out at 8,113 ft-lb at 4,000 ICE engine RPM—isn’t just high at low vehicle speeds, and drops off once you hit the highway (or vice versa). Instead, for better drivability, Koenigsegg wanted the vehicle to have lots of thrust whether the driver is traveling at low or high speeds. “The Gemera will even have over [1,180 lb-ft] of torque ‘left’ at [217 mph],” the company claims. You can get an idea of how the company managed that via its plot below.

Koenigsegg says in its press materials that adding up all the electric motors would get you 1,400 horsepower of theoretical power output, but as a combined system with battery limitations and gearing consideration, max output is 1,100 HP, or about 820 kW as shown at the “max electric power” point in the plot above, which occurs at around 220 km/h (or ~137 mph).
You’ll see that the maximum power output of the ICE (labeled “max. ICE power,” which is 600 HP or 440 kW) happens at about 7,500 engine RPM, which —because the front differential is geared so tall—corresponds to a vehicle speed of about 360 km/h, or around 224 mph. This is a significantly higher speed than where the electric power output is maximized,and it’s because the ICE and electric peak power points don’t occur at the same vehicle speed that overall combined output isn’t maximized. Still, the vehicle has a broad torque curve across its speed range.
You’ll also notice in the plot above that the ICE torque curve (in grey) has a dotted curve called “TC Torque ICE.” This considers the torque multiplication from the “HydraCoup,” which I’ll describe in a bit. Koenigsegg actually factors in the HydraCoup torque converter in its overall 3,500 Nm (2,581 lb-ft) “max achievable combined torque” that the company quotes in all of its media literature. “Total output 1700 bhp – 3500 Nm, including Hydracoup,” the company writes on its website. This, I find, is a bit odd, since few automakers that I know of have ever quoted their max torque output to include their torque converter ratio.
HydraCoup Instead Of A Multi-Speed Gearbox
The Koenigsegg Gemera does not have a multi-speed transmission. As previously shown, the rear motors have a single 3.3:1parallelgear reduction, and a three-cylinder engine with an electric motor mounted to its crankshaft sends power to a singlegear reduction in the front differential. Just before power gets to the front diff, it’s sent via a long driveshaft to what Koenigsegg calls a HydraCoup.
Christian von Koenigsegg gives a great description of how it works in the video above from The Drive. The gist of it is that HydraCoup is a fancy, lightweight, machined aluminum torque converter. (If you’d like a description of how a torque converter works, read our explainer).

A torque converter is a fluid coupling that allows for differential rotational speed and differential torque between its input and output. (It’s what prevents your wheels from stalling your engine when your car comes to a complete stop.)
In the case of the Gemera, a driveshaft from the engine and its attached electric motor is the input. It spins the impeller side of the torque converter, which consists of a bunch of specially-designed veins (shown above) that pump fluid against the blades of a turbine. The viscous forces from the impeller spin the turbine (Koenigsegg is pointing to the turbine below), which is mechanically attached to an output shaft, or in this case, to the rear differential.
A stator between the impeller (that’s the input, which spins at the same rate as the driveshaft) and the turbine (the output, which spins at the same rate as the differential input) acts to strategically direct the fluid flow between the two halves of the torque converter to maximize torque converter efficiency.

There are a number of benefits to using a torque converter. First, it allows for a torque multiplication of 2:1 at low vehicle speeds (at engine speeds up to 3,000 RPM). This is critical, because the Gemera’s 2.7:1 front axle ratio is so tall that wheel torque, and thus launch acceleration, would be rather low if the torque from the engine and crankshaft motor weren’t assisted.
For the record, Koenigsegg told me that I was wrong about the front axle ratio being tall, saying, “No, it is not tall, it is correct.”

In some ways, this is accomplishing the same thing as multi-speed transmission. Except, instead of a short first gear multiplying the torque to increase low-speed acceleration, the Gemera is using a fluid coupling, as Koenigsegg writes on its website:
Torque is crucial, especially when accelerating to extreme speeds in one gear. In the Gemera, this is facilitated by the torque-converting HydraCoup – it converts the combined 1100 Nm coming from the TFG and front e-motor to almost double its torque up to 3000 rpm. That is why the Gemera has 3500 Nm of torque from standstill and why it can accelerate from 0-400 km/h in a single gear.
While using a fluid coupling to multiply torque instead of a short gear is less efficient due to losses associated with fluid shearing, Koenigsegg says the efficiency drop is fine, since it’s only used during low-speed, short-duration acceleration conditions. On the freeway or when the driver doesn’t need to accelerate as quickly, things are different. Instead of a taller gear like what a traditional car might use, the Gemera just locks up the torque converter so that the input (impeller) no longer spins at a higher rate than the output to the rear diff (the turbine). They spin together, a setup that Koenigsegg claims actually yields fewer losses than sending power through a tall gear set like one in a transmission. The lockup clutch—which, it’s worth mentioning, is pretty normal to find in standard automatic transmissions—is what allows for regenerative braking through the torque converter to the electric motor on the crankshaft.

“Providing ultimate response from standstill to top speed in the form of a single gear direct drive at lower weight and higher efficiency than what any other hybrid solution can offer,” is Koenigsegg’s justification for HydraCoup over a traditional transmission. The company goes into further detail on its website:
During highway travel, for instance, the KDD reduces drivetrain losses compared to traditional transmissions or CVT by 3-5% as there is no step-up or step-down gear working in series with the final drive – just direct power from the engine to the wheels with the torque-converting HydraCoup locked up.
This setup of a torque converter used in series with a gear reduction is what Koenigsegg calls “Koenigsegg Direct Drive.” The system, also used on the hybrid Regera two seater, is all about weight reduction and simplicity.
“Tiny Friendly Giant” Three-Cylinder Twin-Turbo Engine

Let’s have a closer look at the three-cylinder Tiny Friendly Giant, an engine named after its compact size but relatively enormous power output. The TFG is a 2.0-liter, all-aluminum inline three mounted front to back in the car. You see it in these pictures leaning over to the side in a slant orientation. This is just on the prototype for packaging reasons; Koenigsegg says “The final version is not slanted – as we were able to improve packaging.” It is outfitted with four valves per cylinder and two turbochargers, and it also has a little ghost on it, per Koenigsegg tradition.
Each of those turbochargers receives exhaust gases from each of the three cylinders, but that doesn’t mean each exhaust port splits off into two exhaust pipes. Actually, there are eight exhaust ports—one per exhaust valve—and they each get their own outlet pipe.
Koenigsegg describes this “two stage turbo system” (which can build up to 29 psi of boost) on its website, writing about how closing all the exhaust valves that feed one of the turbos (I’ll describe how that’s done in a moment) yields essentially twice the flow to the other turbo, allowing the engine to build boost faster at low engine speeds:
…one turbo is connected to three exhaust valves – one from each cylinder. The second turbo is connected to the other three exhaust valves. During low rpm and part to high load, all exhaust gasses are pushed to only one turbo, by only opening one exhaust valve per cylinder – thereby doubling the exhaust gases to that turbine. When adequate boost is reached, the second exhaust valve is opened to start the second turbo.

The results speak for themselves. The dry sump-lubricated, coil-on-plug-ignition (this is not unusual on most cars) 2.0-liter engine’s long block—that’s the full rotating assembly plus block, heads, and valvetrain, minus things like the intake and exhaust system, fuel system components, and accessories—weighs only 154 pounds and apparently fits in a “typical carry-on luggage case.” Ford advertised similar packaging when it debuted the 1.0-liter three-cylinder EcoBoost.
The difference is that while Koenigsegg’s engine has all of the lightweight and small size advantages of a three-cylinder, it has the power of a much larger engine. Despite this diminutive size, it makes 295 lb-ft of torque at only 1,700 RPM, and cranks out a maximum of 443 lb-ft between 2,000 RPM and 7,000 RPM before making its peak power of 600 HP at 7,500 RPM and reaching redline at 8,500 RPM.
In naturally aspirated form, the engine makes half that horsepower at 300 and less than half the torque 184 lb-ft, so clearly the boost is making a big difference. As it sits, the automaker claims the Tiny Friendly Giant is “the most powerful engine per cylinder and volume to date.”

This car is interesting enough that I’m even going to talk about the belts on the engine. The accessory drive, shown in the photo at the top of this section, is small. It’s a dual-plane setup, with one belt connected to an an oil pump that acts as a dry sump scavenge pump and main oil pump, and the other to a compressor. That compressor, you can see in the image above, sends compressed air into the cover for the computer-controlled camless valve actuation system that I’ll describe in a moment.

Despite being small at only 2.0-liters, the cylinders themselves are actually rather large. The Tiny Friendly Giant has a slightly oversquare configuration with a bore of 95mm and a stroke of 93.5 mm stroke. This, and especially the special titanium exhaust, apparently helps give the little motor the sound of a larger one, the automaker claims.
Here’s what Koenigsegg has to say about the titanium exhaust and how the little three-pot cub sounds like a full-grown lion:
Fitted with a custom titanium Akrapovič exhaust, the TFG’s 2-liter three-cylinder engine gives lag-free response and comes with an evocative and deep-throated growl. The TFG may be a small engine but it has a big and “thumpy” sound thanks to its large bore and stroke, combined with the “open” sound of Freevalves. The result is a deep, throaty, responsive and alluring sounding engine. The sound can also be smooth as the exhaust notes can be tuned and balanced by the Freevalve system.
“Freevalve” Camshaft-less Engine
The Koenigsegg Gemera’s does not have a camshaft. This is a big deal, because pretty much every production four-stroke piston engine ever designed uses a cam to control valve timing. (Pneumatic valves are F1 tech, but with traditional cams, if you’re curious.) If it’s not clear what that means, here’s a basic refresher:
The location of a piston in the cylinder of a typical internal combustion engine is dictated by the angle of rotation of the crankshaft, since the piston is connected to the crankshaft via a connecting rod. Intake and exhaust valves must open and close at a specific time relative to a piston’s stroke in the cylinder. For example, an intake valve must be open from when a piston reaches about the top of its stroke until it reaches about the bottom. This is the intake stroke. Another example: All valves must be closed when the piston is at about bottom dead center until about top dead center. This is the compression stroke. One way to make this work is to use pushrods running all the way along the engine from the crankshaft to the valve, but pretty much all modern engines control the valves with a camshaft, which is mechanically linked to the crankshaft via a belt or chain or in very rare cases gears, if your engine was designed by a fiend for complexity.
It’s this connection between the crankshaft (which dictates piston position) and camshaft (which dictates valve position) that ensures proper valve timing relative to the piston’s position in the cylinder.
Many modern automobiles have incorporated something called variable valve timing, variable valve lift, or even variable valve duration. Generally, these use electrohydraulic actuators to do either cam changing or cam phasing. Cam changing is to change to a different camshaft lobe profile with a different lift or duration—the lobe below shows how geometry affects those two. Cam phasing is to change when the camshaft opens the valves relative to the piston position by altering the relative angular position between the cam lobe and its sprocket that connects to the crankshaft via a timing belt/chain.

There are numerous advantages to altering when valves open in the combustion cycle, how far they open, and how long they remain open. The main ones revolve around increasing volumetric efficiency for better fuel economy, power, and emissions, as well as drivability (i.e. broadening the torque band across the rev range).
While many modern variable valve timing/lift/duration systems are run by computers, those computers control hydraulic actuators that usually rotate a part of the camshaft or trigger a metal pin to lock in a specific camshaft profile—the systems are largely mechanical, and therefore quite limited in how precisely and how quickly they can function.
Koenigsegg’s Freevalve, also called “fully variable valve actuation,” is different in that instead of a computer controlling an actuator that changes the shape/angle of a camshaft to alter the valves’ motion, a computer controls a pneumatic actuator that acts directly on each valve. This allows Koenigsegg to precisely and quickly vary each individual valve’s lift, duration, and timing. “Both the intake and exhaust valves can be opened and closed at any desired crankshaft angle and to any desired lift height,” the company writes on its website.
Koenigsegg describes the setup further:
For any engine load criteria, the timing of intake and exhaust can be independently adjusted. The system can then “decide” how to operate the valves depending on driving conditions – which combination to use in order to maximize performance, minimize fuel consumption or regulate emissions. Freevalves allows for a greater degree of control over the engine, which in turn provides significant performance and environmental benefits.
The company claims a fuel consumption 15 to 20 percent lower than “a typical modern four-cylinder two-liter engine with direct injection and variable camshaft.” Part of the reason is that there’s no throttle (and thus no pumping losses associated with one) needed to regulate airflow to the engine, since the valves themselves can now do this with precision. Another way that Freevalve helps reduce fuel consumption, Koenigsegg says, is that it allows the Tiny Friendly Giant to deactivate certain cylinders with something called “Frequency Modulated Torque.”

The Swedish maker of absurdly complex cars doesn’t go into detail on what this is, but I did find more in the patent on this tech from Freevalve. (Freevalve is Koenigsegg’s sister company, and was formerly called Cargine Engineering AB.) Freevalve explains that its system uses the engine’s intake and exhaust valves to precisely alter which cylinder fires and when in order to yield the requested torque in a smooth and efficient way. From the patent:
A control method for modulating the torque in an internal combustion engine with mechanical power transmission and with pneumatically, hydraulically or electromagnetically controllable valves that are open and closed based on signals from a control system, by which method a torque that is requested in an operative situation at a certain moment is provided by a selection of the frequency with which power strokes are performed by controlling the number of power strokes in relation to the number of idle strokes. The power strokes take part in 2-stroke cycles or 4-stroke cycles, and one or more 2-stroke cycles are alternated with or more 4-stroke cycles.
The patent describes what it means by “frequency with which power strokes are performed,” writing:
Power stroke is referred to as a stroke in which the energy of a mass of gas that is expanding after combustion is transformed to mechanical work…
Here, idle stroke is referred to as a stroke in which there is no gas exchange, and no supply of air or combustion, and in which, thereby, there is no positive work being performed during what would otherwise have been a power stroke. This results in a minimum of friction and heat losses. During an idle stroke, no air, or air and remaining fuel is pumped through the engine. An idle stroke requires that at least the inlet valves are controllable, in order to be kept closed for the purpose of preventing air from being introduced until they are opened; however the invention is as most advantageous if also the outlet valves are controllable.
The power stroke frequency may vary between 0 and 100 percent of the relevant number of revolutions per minute of the engine. A frequency can be selected by determining that a power stroke shall be performed every n revolution.
I should make clear that it’s not just Koenigsegg that’s doing this fun stuff. This all sounds very similar to major auto supplier Delphi’s “Dynamic Skip Fire,” which Chevy calls “Dynamic Fuel Management”—a variable cylinder deactivation strategy that precisely chooses which cylinders to fire via precise control of intake and exhaust valves.
In addition to the increased volumetric efficiency associated with granular control of valve lift, duration, and timing, as well as the benefits of valve-controlled cylinder deactivation, Freevalve also allows the Tiny Friendly Giant to run the Miller Cycle to effectively vary its compression ratio for improved efficiency. Fans of 1990s Mazdas, which introduced most of the world to Miller Cycle engines, will be perking up at the moment.

This cycle involves closing an intake valve late such that, as the piston moves up during the “compression stroke,” it actually pushes some air/fuel out before actually doing the compressing. This yields a lower effective compression ratio (the engine’s static compression is 9.5:1, which Koenigsegg says “is high for a high boost turbo engine”), and one that is lower than the expansion ratio. This allows for more work to be extracted from the air and fuel, as Car & Driver describes in an article on the similar Atkinson cycle (a name often used interchangeably with Miller cycle):
The Atkinson cycle delays the intake valve’s closing until the piston has completed 20 to 30 percent of its upward travel on the compression stroke. As a result, some of the fresh charge is driven back into the intake manifold by the rising piston so the cylinder is never completely filled (hence the low-speed power reduction). The payoff comes after ignition when the piston begins descending on the expansion (also called power) stroke. Consistent with Atkinson’s original thinking, the shortened intake stroke combined with a full-length expansion stroke squeezes more work out of every increment of fuel.
Koenigsegg also mentions cold-start benefits, saying traditional cars produce quite a bit of pollution in their first 20 seconds of running, as the catalytic converters aren’t as effective when cold, fuel struggles to mix, and chilly cylinders don’t help the situation any, either. The Tiny Friendly giant apparently has answers:
The TFG overcomes two of the three issues directly at start up, by heating up and provoking turbulence of the fuel mixture back and forth through the intake and exhaust valves. This much-improved cold combustion also leads to much faster catalytic converter heat up, thereby reducing cold-start emission by around 60% compared to an equal-sized traditional engine with camshafts.

Koenigsegg goes further into detail on how Freevalve helps with cold starts, especially when using alcohol fuels (a big selling point to this hybrid is its environmental friendliness, including its ability to use “renewable alcohol fuels”), which are apparently more difficult to vaporize than gasoline and which typically require gasoline to be mixed in to get a good cold crank. Specifically, the company mentions internal exhaust gas recirculation (opening the exhaust valve to suck hot exhaust gases back into the cylinder during the intake stroke), an ability to change compression ratio, special valve actuation to facilitate mixing, and a “heating mode” that cranks the engine a bunch of times to use the piston as a pump to increasing inlet air temperature:
The Freevalve system overcomes this cold start issue by utilizing a pre-start heating mode for the initial cranking and first combustion. One intake valve is used and opened late with low lift for maximum turbulence and vaporization. Cylinder deactivation is applied to increase the amount of air and fuel in each combustion during starting and warm-up. Internal exhaust gas recirculation (EGR) is activated in the following combustion cycles, using hot residuals from the previous combustion to vaporize the fuel. Lastly, the engine’s variable compression ratio is adjusted by the Miller cycle.
Furthermore, the TFG can be turned multiple times before turning on the ignition, using the piston to pump the air back and forth to the inlet in a “Heating Mode” cycle. The result – the inlet air temperature is increased by 30˚ C in 10 cycles (taking about 2 seconds) and without need to add petrol to the fuel or starting cycle anymore, making the TFG fossil fuel independent in any climate.
It might seem a bit odd that a 1,700 horsepower car is using the Miller cycle and worrying about warming up catalysts, but the reality is that even supercar manufacturers have to pass emissions regulations. Not to mention, it’s 2020, and buyers of high-end cars expect more than just fire-breathing big-block gas engines. Clean is now cool.
Jason Fenske from Engineering explains breaks down Freevalve very nicely with his video, showing the pneumatic method of actuating valves, and how hydraulic oil is used to stabilize a certain valve position and to damp its motion:
Frank Markus from Motor Trend breaks down the mechanical bits simply, writing:
…compressed air opens the valve almost instantly, electronically controlled hydraulic pressure holds it open, a coil spring closes it, and passive hydraulic pressure cushions its “landing.” An electric coil provides highly precise sensing of each valve’s position.
Markus also spoke with Freevalve marketing director Andreas Möller to learn about the power draw of Freevalve, which is a significant drawback:
The second major concern is the one that generally doomed these systems in the past: energy draw. Möller says that although the compressor (featuring standard AC-compressor innards capable of peak pressures near 300 psi) generally consumes more energy than camshafts, this is partially offset by a reduction of the engine oil flow and pressure required to lubricate cams and valves. (Freevalve’s head employs a dedicated hydraulic circuit.) And Freevalve’s high-speed friction penalty is countered by the fact that at idle and lower speeds its parasitic losses undercut those of several VVT systems.
I reached out to some auto engineers to get their opinions on Koenigsegg’s Freevalve technology. One engineer, who used to work for a major supplier on timing drives, admitted that he may have some concerns about reliability and cost, but on the plus side, the system could be more forgiving if timing is off. (Indeed, Motor Trend confirmed that a piston will not break the valve if timing is off.) He also mentioned other benefits of ditching all those valvetrain parts, writing about rotational inertia in his email:
It greatly simplifies engine design since you don’t have account for a timing drive and the associated resonance dynamics it brings with it. I don’t know how it compares weight-wise to a timing drive, but it certainly has a lot less rotating inertia to worry about (no cams, chains, or heavy vct units to worry about, so it can react quicker).
A powertrain R&D engineer at a major OEM who asked not to be named also gave me his thoughts, saying:
There are certainly a lot of benefits to having a flexible valvetrain, like the ability to …retain internal exhaust gas residuals for intake charge heating and dilution (NOx reduction & de-throttling), while still having cam profiles that can trap a lot of air at high loads while keeping the intake open late to give up some compression ratio for high maximum power and knock reduction. Turning off one of the intake valves for increased swirl is also a well-known idea that has been implemented in production as well. So, fundamentally the concept and idea is sound.
None of this is new though; this is the motivation behind adding cam phasers, Honda’s VTEC (yo), BMW’s Valvetronic, FCA’s Multi-Air, and all sorts of switchable cam profiles, slide-cam, switchable roller-finger-followers etc. Of all of these systems, most of them are discrete, having two or three defined positions and profiles instead of a continuously variable range (Cam phasing, Valvetronic and Multi-Air are continuous mechanisms in one dimension – they only affect phasing, not lift profile, or they affect both but in a well-defined relationship). Most manufacturers stick to discrete systems or limit the number of continuous dimensions for three reasons:
First, its cheaper to develop and produce discrete-step mechanisms.
Second, it’s much easier to diagnose discrete-step mechanisms, specifically for OBD-II requirements. For the mechanism to be OBD-compliant, there needs to be some sort of feedback to the computer, either through an internal model or an actual sensor, to determine whether the mechanism is working as-intended since it’s proper operation is necessary to maintain emissions compliance. A continuous-action mechanism generally needs a much more complicated and expensive sensing setup to ensure that it is working as intended.
Third, if you choose the discrete valve profiles and cam phasing angles well, you can get 99% of the same benefits as a fully flexible valvetrain. Even with advanced combustion modes like HCCI and SPCCI that rely heavily on internal residuals and precise valvetrain control, conventional systems are still capable of performing well.
He went on, saying that, while Freevalve should allow for faster opening and closing rates at lower engine speeds than cam-driven valve, he doesn’t think this a huge advantage over conventional systems. At high RPM, faster closing valves could provide more of a benefit, but “you’re still limited by the valve spring stiffness, valve mass, and seating rates to avoid physically damaging components,” he told me via email.
In addition, he also mentioned losses from the pneumatic pump that actuates the valves, and the complexity of the OBD requirements, which will necessitate significantly more channels to be monitored. He ultimately concluded by saying that the setup is really best used on a pricey car like the Koenigsegg:
So, in summary, it’s a complicated, expensive way of doing something that all major manufacturers are already doing, and the incremental benefits only make sense for a supercar where the additional cost & complexity is inconsequential, especially compared to the bragging rights that could come with it.

Indeed, the whole Freevalve setup—which reduces engine height thanks to a lack of overhead camshafts—is ridiculously complex, which is why Koenigsegg hired an artificial intelligence expert called SparkCognition, a company out of Austin, Texas. Just read all of these variables that play into Freevalve, and you’ll understand why. From Koenigsegg:
There are many variables at play in the workings of an internal combustion engine (ICE). These include the complexity of achieving maximum performance, efficiency, reliability and safety with minimum fuel consumption, emission, size and cost.
… The Freevalve system creates many more variables to consider and tune. These can include NOx, CO2 emissions, fuel consumption, HC/NMOG, power and torque, all competing for priority in a cycle…Then there’s fuel types, lubricants, temperatures, component wear and tear, alongside the Freevalve liberation.
Clearly it becomes virtually impossible for humans to tune each parameter for optimum results. Given this, Koenigsegg has decided to use AI in order to optimize the TFG for different conditions and situations
Koenigsegg claims its engine is capable of running at efficiencies up to 50 percent while cruising.
Body And Aerodynamics

The Koenigsegg Gemera is a four-seater, but it has no B-pillar and only two doors, which—as you might imagine—are rather enormous, spanning much of the car’s roughly 118-inches of wheelbase. Those doors are are among the Gemera’s most grabby features, with the automaker calling them “Koenigsegg Automated Twisted Synchrohelix Actuation Doors” (KASAD), a slightly altered variant of the “Dihedral Synchro-Helix Doors” that the company has used for years.
They pop out, lean forward, and even raise up a bit as they rotate roughly 90 degrees such as the rearmost part of the closed door reaches high in the sky when open (there are sensors that will prevent it from banging a parking garage, Koenigsegg makes clear). Koenigsegg told me over email that KASAD uses the same parts as the older Dihedral Synchro-Helix design, but now the doors lift up a bit to clear curbs. From the automaker:
KATSAD is our new patent first implemented in the Jesko, where we managed to twist/bend the main components so that the door also swings upwards – not only outwards and rotating, but also upwards. This was possible without adding any new parts – just changing the geometry so we can can clear really high curbs, making the door system even more practical.

You can see the basic operating principles behind how the Dihedral Synchro-Helix doors work in this video excerpt from The Drive. I don’t have a close-up of the new KASAD setup, but it’s apparently quite similar:
“The KATSAD has a very small opening footprint,” Koenigsegg writes about the door’s advantages, “which allows effortless access even when parked with limited surrounding space.” The long door and lack of B-pillar improves ingress/egress for the rear passengers.
Those doors are fastened to a completely carbon fiber monocoque chassis (the body panels are also all made of carbon fiber) with torsional stiffness of 40 KNm of torque per degree of deflection from axle to axle. I don’t know how that compares to other cars, but Koenigsegg is convinced this makes the Gemera the stiffest four-seater sports car on earth.

As for aerodynamics, you can see openings just before ahead of the headlights; This area of the car is a high pressure zone, and the area in the wheel openings is a low pressure zone, so air flows readily from under the headlamps towards the wheel arches to cool the brakes during aggressive driving. It’s worth mentioning that regenerative braking takes some of the heat load off the friction brakes.
You’ll also notice a gaping frontal opening, small vents at the edges of the front bumper, two ducts in the hood, an opening behind the side glass on each side, and one opening just behind each door. Koenigsegg told me via email that the frontal opening helps cool the engine, battery, and HydraCoup unit, and contains a condenser for the AC system. The hood vents and those in front of the doors are exhausters that reduce the pressure aft of the front heat exchangers to help facilitate airflow through them. As for the vents on the edges of the front bumper, they’re there to create “air curtains” to reduce drag created by the front wheels.
If I understood Koenigsegg correctly, the little opening on the side behind the passenger compartment is the engine intake, while the big side opening is there to get air to coolers for the rear motor gearboxes and the engine intercooler.

In the rear, there are openings above the engine bay near each exhaust pipe. Those outlets, Koenigsegg says, allow for natural convection to cool the engine bay. While driving, they, along with the vents under the taillights and ducktail, extract hot air from the engine compartment due to the lower pressure at the rear of the car.
The two giant openings in the bumper are the main exhausters for the rear heat exchangers, which include the transmission (gear reduction) cooler and low temperature radiator for the intercooler. “At slow speed operation there are fans in the rear engine compartment for most coolers and compartment as a whole,” the company’s engineers told me.
The last aerodynamic, but also rather gadget-y feature, are the side mirrors, which are actually cameras. They’re not legal in the U.S., so whichever person buys one of the 300 Gemeras built and brings it to the U.S. will get regular mirrors.
Suspension, Steering, Brakes

Front and rear aluminum subframes are hard mounted to the carbon fiber chassis, and suspension components mount directly to those subframes. The suspension, by the way, is a double wishbone setup with electronically adjustable damping and ride height.
Steering is an electric rack and pinion setup, and there’s active steering in the rear, which Koenigsegg says helps “shrink” the car’s wheelbase, so to speak. Helping slow down the carbon fiber wheels are six-ceramic-piston calipers on 16.3-inch diameter ceramic discs up front and four-piston grabbers on 15.3-inch plates in the rear.
The Gemera, like most electrified vehicles, also offers regenerative braking, and in this case, it “starts at throttle lift and increase while braking,” per Koenigsegg.
The Batteries

The 800-volt battery on the Koenigsegg Gemera is only 15 kWh, and offers an EV-only range of up to 31 miles max, which combines with 590 miles of ICE/electric hybrid range to give the car up to 621 miles of total reach.
The idea behind using such a small battery, von Koenigsegg says, has to do with minimizing weight. “Electric cars are great,” he says in the video below, “but there are not enough charging stations around, and it’s difficult to produce cells quickly enough for worldwide implementation. So, this is a parallel track, where you get a lighter car…”
How light? Well, he says the goal weight is around 1,880 kg, or around 4,144 pounds. That sounds like a lot on its own, but, for the record, is about 1,000 pounds lighter than the all-electric (but largely carbon fiber-less) Porsche Taycan four-door.
“You get a more agile, roomier car with better acceleration, better cornering, better braking, still CO2 neutral if you find the right fuel.”
The pack is made up of liquid-cooled pouch cells. You can see the coolant ports at the front end of the car in the picture before the video directly above. I also point out the two power inverters that turn DC from the battery to AC for the motors, as well as the high voltage plugs on those motors. Battery pack max discharge power is 900 kw, while max recharge capability is 200 kW. The charge port is just behind the side door, on the opposite side of the fuel filler.
I could go on and on about the technology in Christian von Koenigsegg’s dream of sharing the Megacar experience with your whole family. (That was the impetus behind this four-door concept.) I could mention the slim carbon fiber seats, the fancy eight cupholders, the beautiful front indicators, the rotating display behind the steering wheel, and on and on. But my editors are already going to kill me when they see how long this story is, so I’ll just end with: The Koenigsegg Gemera will go into production in 2022.
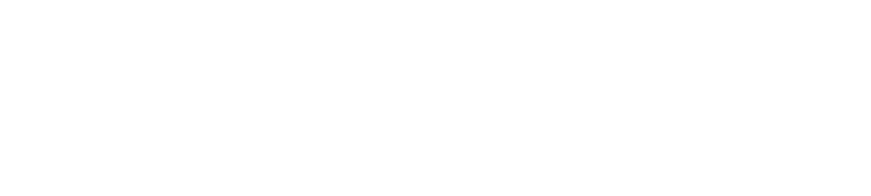