Plenty of auto manufacturers are known for high-tech factories that make halo cars. But usually those facilities are in Europe, like Bugatti’s sparkling white plant in France or McLaren’s incredible speed laboratory in England. Acura would like you to change your thinking here, one of the most advanced car factories in the world can be found in America’s heartland.
(Full Disclosure: Acura recently invited Jalopnik to Ohio check out their full lineup, with a focus on the updated 2019 ILX and NSX models, but wanted to take us on a special tour of the Performance Manufacturing Center in Marysville, Ohio. I also used to own a 1992 NSX ages ago, and worked for Acura from 2002 until 2005, when I worked in dealer operations in sales and fixed operations leadership.)
From 1990 until 2005, Acura produced the NSX in their obsessively clean and meticulously operated factory in Takanezawa, in Tochigi Prefecture, Japan.
With the introduction of the 2017 NSX, Acura wanted to shift focus to the American talent responsible for nearly all of the lineup’s cars—only the RLX is built in Japan— to show off how worthy its work is by building the NSX in Ohio.
I went there and had a look, and walked away in awe.
Advertisement
Exotic Car Plants Have To Be Special
There are plenty who will say there has been another supercar factory in Bowling Green, Kentucky since 1981, but that place is just another GM plant, filled with robots and assisted machinery. It just happens to be the place where Chevrolet makes the Corvette. (We’ll know more about whether we can add it to the supercar list when the mid-engine Corvette drops.)
The Performance Manufacturing Center is different. The Marysville, Ohio plant is purpose built for the NSX, and inside it looks the part for an exotic car. When you first walk in, you notice it’s one giant open room, and that there are no assembly lines and very few robots. Instead the cars move from station to station on carts, and that people do the vast majority of the work by hand. Everything is white, including the staff’s clothing, and the lighting is supplied by clean LEDs. It’s all very clinical.
Employees go through a rigorous selection process, including written exams and interviews, to prove that they’re above the usual cut of factory workers. Just over 100 technicians work inside the PMC, and do so in four 10-hour shifts.
Advertisement
This schedule and setup is first for Honda or Acura. Delivering eight cars per day, on average, the plant seems rather productive considering how much work is done by hand. Acura’s NSX GT3 cars are also produced in this plant, right alongside the road cars.
Refreshingly Simple
The plant manager was quick to encourage me to take pictures everywhere. Nothing was off limits.
As I was escorted from station to station, I loved that I didn’t have to wear any ear protection, and wasn’t required to yell in order to communicate my hosts. At a quick glance, everything appeared spotless, no matter which section of the plant we were in.
Most car plants are loaded with tooling, robots, and noise. The Performance Manufacturing Center is surprisingly quiet and clear of clutter. With only frame welding, riveting, windscreen installation, and paint processes completed by machines, human hands do the rest of the work assembling the NSX with an inside-out method.
Advertisement
All of the interior components and electrical systems are installed in the early stages, and then the team works on assembling the body. With tons of tech and batteries needed for the hybrid system, it makes sense to work this way.
A Few Changes In Ohio
One gripe about older-generation NSX was the paint quality between the metal and composite pieces, as they were painted in different locations, and this would show over time.
Advertisement
With the new NSX, all parts are painted in the same location, at the same time. Keeping consistency and quality at a high level is important. Priming work is done by hand, but Acura takes the paint guns out of human hands, since a robot’s motion is perfectly calculated for even coverage.
Customers have the option to participate in the completion of their NSX, with the team allowing them to put finishing touches on their car alongside the technicians. Of course, it’s a simple task like a wheel nut or small screw, as the techs get to do the important stuff.
As assembly completes, final checks for alignment and wheel & tire balance are done before shakedown tests on the dyno. After the dyno pulls and braking tests, each NSX goes into the shaker room, where it runs for hours to see how well the suspension responds while ensuring quality installation of any would-be rattling interior fasteners.
Advertisement
If the car fails any tests at all, even in the smallest margin of error, it gets sent back to the station for correction before another test.
Some Epic Results
Acura rolled the dice by making the switch from Japan to Ohio for building their halo car, and as we’ve tested on Jalopnik, the end result is impressive.
Advertisement
After eeing how the new NSX moved from station to station, throughout its assembly at the PMC, I was anxious to check it out for myself. Luckily, Acura made arrangements for me to take it to some local proving grounds, where I made sure to put it through its paces to see how much better it is for 2019.
Turns out the product is just as good as the factory itself. Which must be the whole point, right?
Advertisement
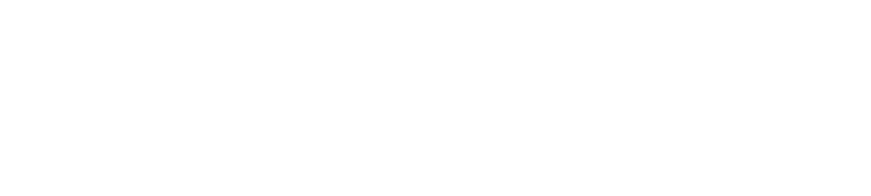