
I’m guessing by now you’ve heard that carmakers have had to slow down or in some cases even stop production because there’s a global shortage of microchips of all kinds. Modern cars are crammed full of these silicon thinking-flakes, so if there aren’t any around, cars won’t get built. This is a strange situation, to be sure, and it’s worth digging into why it’s happening. So let’s do that.
There’s been a number of explainers out there, and they all generally arrive at the same conclusions, because, well, everyone can pretty clearly see what went wrong. And unsurprisingly, a lot of the blame can be placed squarely on the thing that we can blame for so much of life’s current shittiness: COVID-19.
Before we get into what’s happening now and complain more about that damn virus, let’s just go over a bit of context and history. Cars have had computers in them since way back in 1968, with Volkswagen’s Type 3, which used a simple electronic computer to manage the fuel injection system.
Since then, cars have been adding computer modules steadily. Modern cars have multiple independent computer modules, controlling the engine management, infotainment systems, stability control/brakes, body functions, HVAC, and more.
Really, it’s kind of amazing. New cars have enough interconnected computers in them that they would have been considered a whole rolling LAN party back in the 1990s.
The bottlenecks in making computer chips in huge quantities aren’t raw material-based, like those of many other manufactured goods would be. Computer chips rely on silicon semiconductors, and silicon is, right after oxygen, the most abundant element on Earth. It’s sand, pretty much.
The problem is complexity. Computer chip factories—often called “fabs”—are incredibly complex and expensive, and getting new factories built takes considerable time and resources, which is why this problem can’t be solved by quickly opening a bunch of new fabs—it’s just not that easy.
Let’s get back to COVID. Among all of the cultural and socioeconomic things that came along with the pandemic, we can point to two that really seem to be at the root of the chip shortage.
First, as the pandemic started and people began to stay at home more, car sales took a huge hit, which caused carmakers to cut orders for new chips from their manufacturers, since they weren’t selling cars.
At the same time, people began spending more time at home, and, significantly, working from home. That caused people to start buying a lot more consumer electronics and computers and game systems and phones and tablets and all of the other equipment of modern life, all of which use plenty of modern microchips.
So, the chip fabs (mostly in Asia; a few in the U.S. and other places) were going at full capacity, cranking out CPUs for iPhones and Playstations and microcontrollers for televisions and videoconference-ready cameras and all sorts of products.
Now, you’d think that carmakers could just buy chips like anyone else, but that’s not really how it works. Even though many modern cars are adopting the same basic ARM CPU architecture that so many phones and game consoles (pretty much everything other than most desktop PCs) use the kinds of chips used for the automotive industry are fundamentally different than consumer electronics-grade chips.
Automotive-use CPUs have to be, among numerous other things, far more forgiving of temperature extremes. You may recall that Tesla once tried to get away with using consumer-grade LCD displays in their cars, and that bit them on the ass.
So, factories are going full-tilt building chips that, fundamentally, car companies can’t use. And it doesn’t matter how deep Toyota or GM’s pockets are, carmakers only account for about 10 percent of global microchip volume, which means they just don’t have the same leverage over the chipmakers as they do with other suppliers.
Brembo, for example, isn’t selling brake calipers to Apple or Sony. They sort of have to do what their carmaker clients want. A big chip company like Foxconn isn’t going to blink an eye if it means ignoring Ford to please Apple.
COVID also caused some production slowdowns in chip fabs across the world as they adapted to the new, crappy reality of pandemic standards, and a fire at Japan-based Renesas Electronics Corp, which makes about 30 percent of the microcontrollers used in the automotive industry, is another contributing factor.

There aren’t a whole lot of bright sides here, and not a lot of easy paths out of this for carmakers. There’s high demand across the board, across so many industries, and only so many capable chip fabs.
So what can be done? Maybe carmakers could re-design computer modules to use lower-tech components, like these old 7400-series TTL chips, that seem to be plentiful? Unfortunately, I think people’s demands have moved too far past what old tech could do, and stepping back isn’t really an option. Plus, I’d imagine there would be some engineering challenges…
I mean, there may be a demand somewhere for cars that don’t use a lot of computers—maybe this is Mahindra’s chance to get the Roxor street-legal and fill that gap!
That’s also unlikely, as is the possibility of harvesting Bill Gates’ mind-control 5G microchips from our Coronavirus vaccines, since I don’t think those are automotive-grade.
The only thing that really makes sense is carmakers accepting that they’ll need to develop a parallel supply chain for microchips that doesn’t overlap with consumer electronic needs.
Money will have to be spent, subsidiaries opened, chip fabs built, all that. Cars are not going to suddenly start requiring fewer chips— the opposite is likely true.
Smart carmakers should be pooling resources and planning to build their own microchip supply chains, with factories dedicated to automotive chip fabrication.
Otherwise, I really don’t see how this won’t happen again and again, and I don’t really see how that would help anybody.
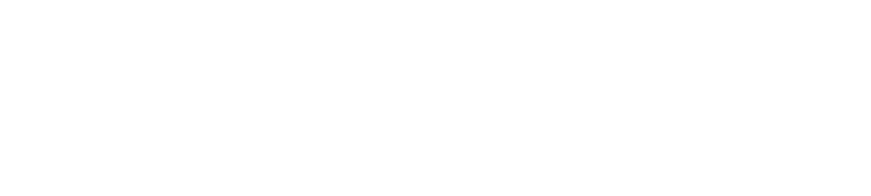