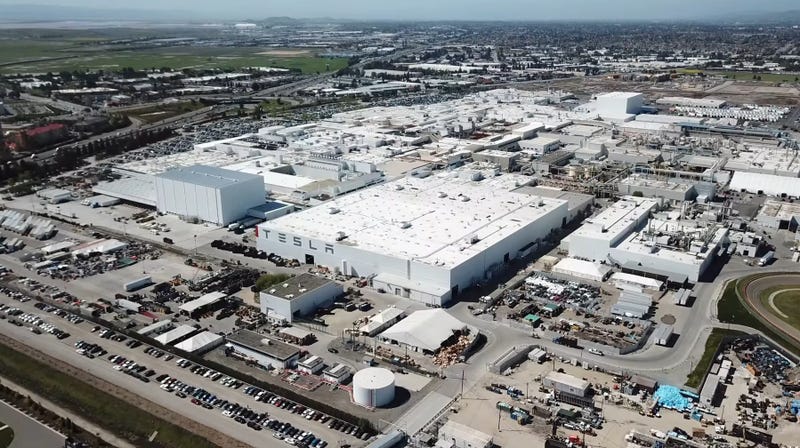
Tesla has been building cars for nearly 15 years, but it’s still learning the best way to do that as it ramps up production of the make-or-break Model 3 to the target of 5,000 cars per month. It’s much more a running work in progress than you might think.
In a recent New York Times feature, Neal Boudette illuminates just how CEO Elon Musk has set the automotive industry on its ear, from his infamous temporary tent assembly line to testing robot breaking points and changing manufacturing techniques mid-stream.
Car production is something that many fledgling companies struggle with. Building cars is an incredibly complex process, and Musk is attempting to institute a wholesale change in the way cars are mass-manufactured. The company seems to be capable of managing the “manufactured” part, it’s the “mass” they’re having trouble with.
In the process of reading this, you start to understand there is a reason other companies don’t operate the way Tesla does.
A recent daylong tour of the Fremont plant revealed how Tesla is trying to break with standard auto-industry practices all along the Model 3 assembly lines. It is searching for ways to shorten the time that robots take to weld parts. It is even making seats, a component most car companies leave to specialized suppliers. And it is doing this while trying to root out bottlenecks and glitches in the manufacturing process.
In the final assembly area, for example, Tesla originally used robotic arms to install the Model 3 seats. But the machinery was slow and inconsistent in tightening the bolts that secure the seats and connecting the wiring that supplies power to them. About a month ago, company officials said, that work station was modified so that robots move the seats into place and workers handle bolts and the fitting of delicate electronic connectors.
Advertisement
Tesla is currently going through the process of learning not how to build a car, but how to build thousands of cars. The existing assembly lines operate too slowly for Elon’s lofty production number goals. The company has ramped up the speed of each step of the process, but problems arise when systems operate at speeds outside of their original range of development.
For example:
At 3 a.m. on Thursday, the time Tesla made him available for a telephone interview, he said he was trying to fix a glitch in the part of the plant where the Model 3 is painted. “The carrier that the car is on is coming out of the paint booth slightly too fast for the sensor to recognize it, and it’s tripping the sensor even though everything is fine,” he explained.
Tesla engineers are trying to reprogram the sensor so it can operate at the accelerated pace. For now, he said, “we have somebody standing there just pressing the ‘O.K.’ button to restart it.”
Advertisement
Workers given menial tasks like this one seem to be something of a norm at Tesla. “One of the biggest mistakes we made was trying to automate things that are super easy for a person to do, but super hard for a robot to do,” Musk said during the company’s June shareholder meeting. “And when you see it, it looks super dumb. And you are like, wow! Why did we do that?”
Combined with a taxing 10-12 hour shift schedule, this could explain the company’s high turnover. Workers easily get burned out, and simply replacing them with new cogs in the machine isn’t as simple as it sounds. The company aims to hire about 400 employees per week to both accelerate manufacturing and outstrip the pace of workers leaving.
“Everyone I talk to has only been here for two weeks, a month, and those people don’t last long,” said Jonathan Galescu, a Model X body repair technician who has worked at the plant for four years.
A manufacturing expert says automakers typically give new workers several weeks of training before putting them into production work. Bringing in large numbers of new workers can hurt quality because they may not perform their work properly or fail to notice when problems crop up.
New workers at the Fremont plant get three days of training before going to work on a production line. This includes a day of computerized virtual training on doing their jobs safely, and a day of instruction on the area to which they will be assigned.
Advertisement
New workers make mistakes simply by dint of being in unfamiliar environments. This constant burnout and replace process can easily contribute to quality issues, and more importantly, safety issues.
But it isn’t just humans stressed beyond the breaking point of Musk’s I-alone-can-fix-this mentality. Even the robots are feeling the strain.
In another bid to push the limits of technology, Tesla at times pulls robots off the line and tests them operating at speeds greater than specified by the supplier, said Charles Mwangi, Tesla’s director of body engineering.
“We are actually breaking them to see what the maximum limit is,” Mr. Mwangi said. The idea is to find ways of accelerating production without spending capital on new machinery. In the future, rather than adding more machines to increase output, “we can just dial up our equipment,” he said.
Advertisement
Where production schedule fixes can’t be found by ramping up human and robot speeds, Tesla has taken to changing the components and processes of building the car itself, emphasis mine below:
For other tasks, the reliance on robots has proved a headache. For months, Tesla engineers struggled to get a robot to guide a bolt through a hole accurately to secure part of the rear brake. They found a maddeningly simple solution: Instead of using a bolt with a flat tip on its threaded end, engineers switched to a bolt with a tapered point, known as a “lead-in,” that can be guided through the hole even if the robot is a millimeter off dead center, Mr. Moravy said.
In a very tangible sense, Tesla views its production line as a laboratory for untested techniques. In recent weeks, company executives concluded they could produce Model 3 underbodies with fewer spot welds than they had been using. The car is still held together by about 5,000 welds, but engineers concluded that some 300 were unnecessary and reprogrammed robots to assemble the steel underbody without them.
Advertisement
Musk is aiming to revolutionize the automotive industry and how cars are manufactured, but it seems he spends a lot of time figuring out solutions to problems that companies like General Motors, Toyota, and Volvo figured out decades ago. It may be time for Elon to extend an olive branch and request Toyota’s expertise in the art of kaizen. Hell, the folks from Toyota probably still have a favorite restaurant in the Fremont area, it may not be too difficult to get them on board.
The Times’ story is very much worth a read in full, and you can check it out here.
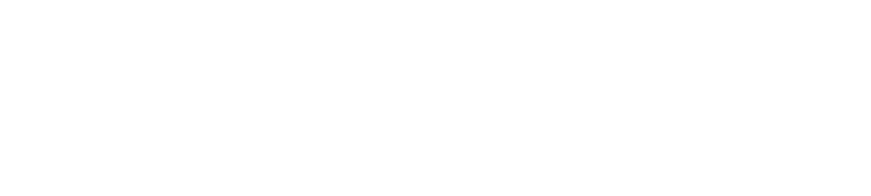