Electric cars are quickly coming into the mainstream, especially in Europe. So, since I was at the Paris Motor Show this week, I figured I’d walk around, look at at all the nice electrified powertrain tech (focusing on cutaway displays), and talk to engineers about what we can expect from the cars of the near future.
I’ve said it probably a hundred times by now, but it’s worth repeating: By and large, true technical innovation in the auto industry generally happens at the supplier level. So most of the folks I spoke with at Paris were companies that sell things not to us consumers, but to automakers.
But before I get to the suppliers’ booths, I have to show you this sweet Jaguar I-Pace chassis, because who would I be if I denied you this EV eye-candy? I’d be a monster, that’s who.
The best part of the model, besides all of it, is the cooling system. Mostly because I’m into cooling systems, but also because just look at where this coolant hose routes:
Advertisement
Advertisement
It goes from the front of the car, just above the motor, into the wheel arch behind where the fender would be, and rearward through the rocker. It’s a bizarre package, but I’m into it.
In the image below shot from the back, you can see that the blue hose makes it back to a box just above the rear motor (I’m assuming this is an inverter):
Here’s a closer look via a Jaguar press photo (notice the blue hose coming from the passenger’s side, there):
Also visible at the front in the photo below is what looks like a high voltage compressor (that big silver cylinder there at the bottom—it doesn’t look dissimilar to an internal combustion engine car’s AC compressor, which tends to be powered by the accessory drive), whose job it is to not only fulfill HVAC functions for cabin comfort, but also to keep cells cool as part of a coolant-to-refrigerant “chiller.”
Advertisement
Advertisement
Normally the I-Pace simply uses passive cooling via a radiator up front, but when cell temps get too high, the chiller cools down the coolant, and thus, the cells.
Speaking of cells, there are 432 of them, and they’re of the pouch variety:
Here’s the closest look I could get:
Advertisement
Advertisement
Speaking of battery packs, major automotive supplier Faurecia—which is French, but has offices all over, including in Auburn Hills, Michigan—showed off its concept for a battery pack made of a composite material instead of aluminum (which many EV automakers are using).
According Faurecia’s Battery Pack Product Line Manager for composite technologies, Guillaume Chambon, a six millimeter battery pack bottom cover can offer the same strength and 50 percent weight savings compared to an aluminum bottom cover of the same thickness.
In addition, the company claims that the insulating property of the composite material allows for more efficient thermal regulation, since nearly all cooling will be acting on the cells, rather than on the external environment. Here’s a look at the cooling path:
Advertisement
Advertisement
That cooling path is under an aluminum plate, which interacts with vertical aluminum plates between cells to make sure that cell heat gets transferred to the coolant.
Here’s a closer look at the small gap where coolant flows under that flat aluminum heat plate:
Notice how there are some aluminum beams between the cells on the left in the image above; those are there for crash protection, I was told. As for impact protection from underneath, Faurecia claims the composite bottom cover (which contains some amount of kevlar) deflects significantly less when exposed to a high load than an aluminum battery pack used by Tesla.
(Obviously, I can’t confirm this; This is based on what a rep told me on the car show floor. He is, of course, making a sales pitch to automakers here, so grain of salt and all that.)
Advertisement
Advertisement
Chambon also mentioned electromagnetic shielding, which requires essentially aluminum foil on the top cover (though other solutions are apparently under development), and some other solution built into the composite bottom cover, perhaps some sort of metal mesh.
Faurecia also brought some fuel cell tech to the party in Paris. Specifically, they set up the two hydrogen fuel tanks above, which they developed with STELIA Aerospace Composites, and which are made of three layers. Starting from the inside, there’s plastic (presumably to help seal), then carbon fiber (for structure), and then fiberglass to protect the carbon fiber.
Faurecia thinks hydrogen fuel cells will take off in the future, in light of battery-electric cars’ weaknesses of weight, range, and charging time. Apparently, the new tanks can be filled in just three to five minutes, and they’re lightweight. The representative told me the 700 bar tanks can fit seven kilograms of hydrogen for 100 kilograms of empty tank mass (Total tank capacity of these, though, is six kilograms). Normally in the industry, he told me, a 100 kilograms tank tends to fit just five kilograms of hydrogen.
Advertisement
Advertisement
The contraption you see there at the end of the tanks include mechanical safety valves, which the rep told me react to temperature (and not pressure), and release hydrogen into the environment as necessary. The valves are also able to tell if there’s a leak in the system, and will shut off flow towards the fuel cell accordingly.
Flow will also be limited by the filling station. In the image before the last, you can see where the fill location is—it looks like a little pole standing up from behind the wheel. A filling station will hook in there, and communicate with the car to ensure that there’s no overtemp situation.
Though before getting to the hydrogen fuel cell stack, the hydrogen flows from the tanks, through this contraption, which drops the pressure from 700 bar to 10 bar.
From there, the hydrogen goes to the 100kW fuel cell stack, where hydrogen ions flow through a catalyst, lose some electrons (which flow through a wire to generate electricity), and then end up combining with oxygen and electrons to form water. Here’s a look at that stack:
Advertisement
Advertisement
In the back here is a small battery pack which acts to power accessories, to recuperate energy during braking, and possibly to power the wheels in high demand situations. The spokesperson pointed out that the battery could also power the vehicle on its own, in which case the vehicle would act as a plug-in hybrid, with the fuel cell stack acting as a range extender.
Next, I headed over to Aisin, a prominent Japanese supplier known mostly for its transmissions, but which is part of a larger group “Aisin Group” that makes all sorts of automotive components.
Among those are brake systems, like the “cooperative regenerative brake system” shown below, which is made by Aisin Group’s Advics, and which is used in the Toyota Prius.
It’s a brake by wire system consisting of an active hydraulic booster on the left, and an “active power supply”—an electric pump and hydraulic accumulator which is meant to store high pressure—on the right.
The basic aim of the system is to ensure smooth, predictable pedal feel even with the electric motor in the vehicle creating drag through its regenerative braking process. Advics describes the main advantage to the system:
Advertisement
Advertisement
An electronically controlled brake system is a control system in hybrid vehicles and so on that utilizes hydraulic brake power and motorized regenerative brake power in a coordinated fashion so that kinetic energy is recovered during deceleration in the most efficient way.
My rudimentary understanding, based on a short discussion with an engineer, is that it works like this:
The driver presses the brake pedal, which pushes the rod labeled “1″ above. This sends fluid into “2,” which looks like a cylindrical chamber. It is here where pedal stroke is measured by the system. Using this information of how much the driver is pressing the pedal, as well as the state of the regenerative braking (i.e. how much the motor is decelerating the vehicle), the ECU (“0″ above) calculates how much friction braking to apply.
If I understand this right, the system applies the brakes by strategically opening valves in “3,” which is supplied by the pump/accumulator. Opening the valves pushes out the piston labeled “4,” which creates pressure in the hydraulic brake system.
The representative told me that there could be times when a driver actually presses the brake pedal, but the standard friction brakes do not activate at all. Rather, regenerative braking is able to yield the appropriate deceleration.
Advertisement
Advertisement
The man at the booth also told me that there’s a safety built in. In case of an electrical failure, apparently a valve in “2″ shuts, diverting fluid directly to the master cylinder, and creating brake pressure.
Also on display at Aisin were a bunch of electric pumps. I won’t dwell on these, since I realize that pumps aren’t sexy. But it’s worth mentioning them, because as cars become more electrified, or as engine stop-start systems continue to proliferate throughout the industry, electric pumps will become more prominent.
If you drive a regular internal combustion engine-powered vehicle, there’s a good chance that your engine coolant is circulated via a water pump on your accessory drive or timing belt/chain, and there’s also a decent chance that your transmission’s fluid moves thanks to its internal geroter pump.
Electric cars don’t have accessory drive belts, so pretty much all the coolant or oil going to the batteries, motors, gearboxes, power electronics, or cabin heaters will have to move via electric pumps. Here’s a look at two (the red and blue “snails” at the bottom of the picture) in the I-Pace shown before:
Advertisement
Advertisement
Even non-electrified cars with engine start/stop need an additional electric pump, since keeping up the line pressure in an automatic transmission is usually done by an oil pump in the trans that spun by the engine, which is off during stop-events. Daimler, in an old press release from 2010 about start/stop, describes this need:
Electric transmission oil pump supplies the clutches of the automatic transmission with oil pressure prior to starting, so as to enable a swift resumption of the journey after direct starting of the combustion engine via the ECO start/stop function
With the engine off during a stop, water won’t flow through the engine or the HVAC system, so cabin heating may be compromised, and an electric pump may be needed to accommodate.
Plus, as fuel economy regulations get tighter, automakers look for ways to increase efficiency, and electric pumps can be switched on and off based on demand, whereas mechanical pumps tend to flow fluid all the time. Some mechanical variable pumps exist, but they’re not as precise.
Advertisement
Advertisement
Aisin also showed me some electric motors, including the 50 kW four-wheel drive unit shown above. It’s basically a liquid-cooled (I can’t remember if it’s oil or water, but you can see the two ports on the left in the photo above) motor integrated into a gearbox. It’s meant to be placed in the rear of a vehicle to assist the front conventionally-driven wheels when necessary, though Aisin says it can power the vehicle all on its own, claiming this eAxle is meant to make it possible to convert a regular ICE car into a plug-in hybrid.
Next to that four-wheel drive unit was the 100 kW electric drive unit you see above. It’s got its inverter sitting on top, meaning this is likely a front drive unit, whereas a rear drive unit might have its inverter on the side, since vertical packaging space below the rear floor tends to be limited.
Speaking of packaging space, Aisin builds its gearboxes for these EVs as planetary reductions or parallel gear reductions, with the former having the output shaft inline with the motor (a shorter but maybe taller overall design), and the latter having it offset but parallel to the motor (a longer design, but possibly flatter).
An interesting thing about this drive unit was a tidbit Aisin electric and hybrid system team leader Takuro Iwase told me. He said that the eAxle above incorporates a dual-cooling system in which liquid coolant (“water”) is used to keep the inverter temperatures down, as well as the temperature of certain parts of the motor (the outside of the stator, if I recall correctly). Other internal components, though, like the rotor, as well as the gearbox itself, are also cooled, but not by coolant—coolant in a gearbox isn’t a good idea—but instead by oil.
Advertisement
Advertisement
That oil in the gearbox grabs the heat of various components, and loses it via an oil to water heat exchanger not shown.
The dual-cooling system is different than the one used in the 150 kW eAxle shown above, in which the motor and gearbox are both oil-cooled. I was told me that this purely-oil-cooled setup allows for a more precise control of oil temperature, but it’s not quite meant for as heavy duty cases as the liquid and oil-cooled design is.
So yeah, that’s what I spent much of yesterday doing: strolling around looking for hardware, and talking to the nerdiest people I could find. It’s what auto shows are for, right?
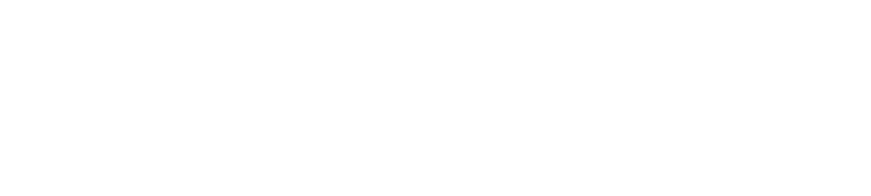