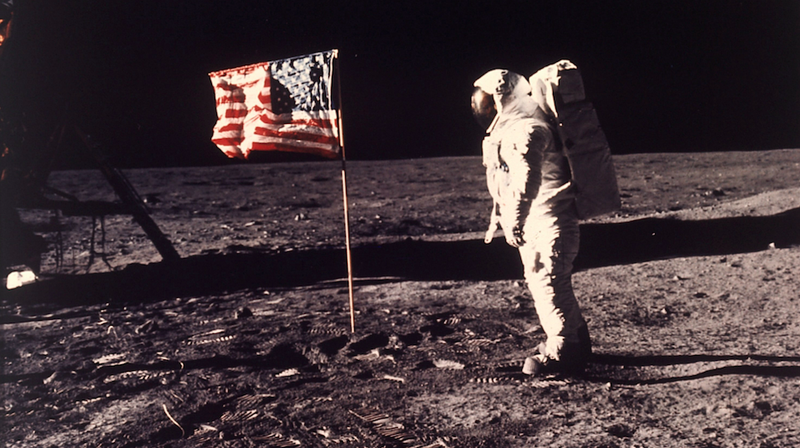
Fifty years ago, American astronauts walked the moon, completing an incredible mission that, if we’re honest, was extremely unlikely to happen as soon as it did. And it was all possible because of incredible innovations, some of which paved the way for new tech in transportation. Here are a few of those innovations.
The Apollo program was a highly controversial one in the U.S. in the 1960s, with only 26 percent of Americans saying that the U.S. should “go all out to beat the Russians in a manned flight to the Moon,” Smithsonian magazine writes. Now, half a century later, I bet most Americans would say it was indeed worthwhile, not just for qualitative reasons like morale, but for more concrete ones like technological development and a greater understanding of how our world works.
Here are a few innovations from Apollo that made their way into the transportation world here on earth.
You Can Thank Neil Armstrong for Fly-by-Wire
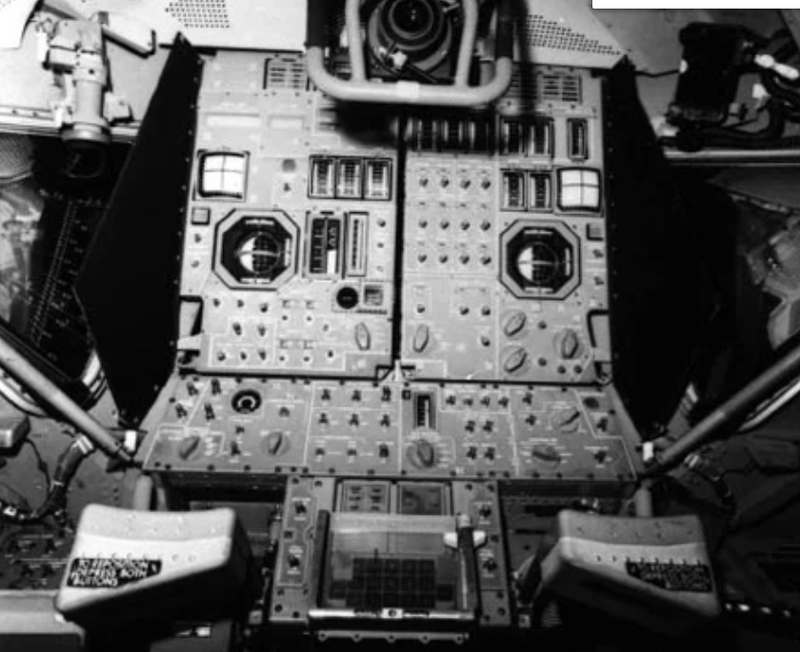
Advertisement
One of the most fascinating innovations coming directly from the Apollo mission—and in fact, from Neil Armstrong and from the first contractor for the Apollo Program, MIT’s Draper Labs—was fly-by wire. From NASA:
Working with other contractors, the [Draper Labs] developed the Apollo Primary Guidance, Navigation, and Control System (PGNCS, pronounced “pings”). Consisting of an inertial measurement unit, optical and other components, the system had at its heart the Apollo Guidance Computer. Designed and programmed by the Lab and largely built by Raytheon, the computer would be the brain for both the Apollo Command Module and the Lunar Module that would deliver the first astronauts to the Moon’s surface. To do this, it had to be faultless.
Advertisement
This Apollo Guidance Computer later came into play after a team from NASA’s Flight Research Center in California proposed an analog fly-by-wire system during a time when most airplanes were controlled by a pilot using sticks and pedals to move pushrods and cables. This was after NASA had developed for the Apollo program a Lunar Landing Training Vehicle—a machine that NASA says was “the first genuine fly-by-wire vehicle.”
After ditching the analog aircraft proposal because it was deemed “too futuristic,” NASA looked into whether a digital computer would work for the task, though the agency initially doubted that there was a digital computer capable controlling an airplane. But it was Neil Armstrong—who had just completed a mission to the moon in which he relied on a digital fly-by-wire system, PGNCS—who let it be known that actually, there was.
Advertisement
As a result, NASA worked with Dryden to adapt PGNCS to airplanes:
Through Armstrong’s support, and that of U.S. Navy Vice Admiral Donald Engen, Dryden acquired a trio of F-8C Crusaders from the Navy and, working with Draper, the Center installed an adapted extra Apollo PGNCS on one of the planes, which became the Digital Fly-by-Wire (DFBW) research aircraft. Another of the F-8s was converted into an “Iron Bird” ground-based simulator for testing the flight software and training pilots, and the third F-8 was used to familiarize test pilots with the aircraft.
Advertisement
The system was first put into full-scale production on the F-16 Viper fighter jet, but fly-by-wire is used on pretty much all commercial airplanes today, and you can thank the Apollo Primary Guidance, Navigation, and Control System for it:
The first commercial airliner to fly with [Digital Fly By Wire] was the Airbus 320 in 1987, followed by Boeing’s 777 in 1994. Today, the technology features in a number of aircraft from both manufacturers. For commercial aircraft, the technology replaces heavy mechanical systems, allowing airlines to benefit from greater fuel efficiency or carry more passengers and cargo. The heightened responsiveness of DFBW-enabled aircraft allows pilots to provide a smoother flight, and the system’s redundancies help ensure safe operation of the vehicle. Mechanical maintenance needs are also reduced, saving costs and time spent on upkeep and repairs of the mechanical systems and reducing the chance of failures.
“Now, when you fly any major, large airplane, you’re flying a digital fly-by-wire system based on the technology from the F-8 program,” says [Darryl Sargent, vice president of programs for Draper].
Advertisement
How the Apollo 1 Tragedy Contributed to Flame-Retardant Racing Suits
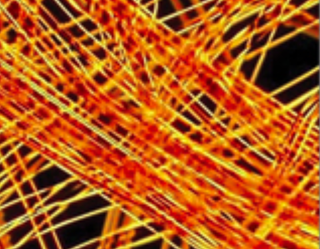
Advertisement
Thermal protection is a big deal for NASA scientists, who have the unfortunate task of having to deal with temperatures as low as -455 °F in deep space, and as high as 2,300 °F during atmospheric reentry, according to NASA.
One material, Polybenzimidazole, or PBI —a thermally stable, non-flammable textile fiber—was the subject of NASA-funded research in the early 1960s, and was quickly brought into use after tragedy struck on Apollo 1 when the pure oxygen atmosphere used at the time in space capsules caught fire, killing the three astronauts inside during a launchpad test:
On January 27, 1967, the severity and immediacy of the danger of fire faced by astronauts was made terribly clear when a flash fire occurred in command module 012 during a launch pad test of the Apollo/Saturn space vehicle being prepared for the first piloted flight, the AS-204 mission (also known as Apollo 1). Three astronauts, Lieutenant Colonel Virgil I. Grissom, a veteran of Mercury and Gemini missions; Lieutenant Colonel Edward H. White II, the astronaut who had performed the first U.S. extravehicular activity during the Gemini program; and Lieutenant Commander Roger B. Chaffee, an astronaut preparing for his first space flight, died in this tragic accident.
Advertisement
This terrible accident led NASA to invest more resources in fire-resistants materials, but with PBI research already underway, the space administration went ahead and used it in flight suits:
NASA contracted with Celanese Corporation, of New York, to develop a line of PBI textiles for use in space suits and vehicles. Celanese engineers developed heat- and flame-resistant PBI fabric based on the fiber for high-temperature applications. The fibers formed from the PBI polymer exhibited a number of highly desirable characteristics, such as inflammability, no melting point, and retention of both strength and flexibility after exposure to flame. The stiff fibers also maintained their integrity when exposed to high heat and were mildew, abrasion, and chemical resistant.
Advertisement
Apparently, NASA used this material for all sorts of stuff:
Throughout the 1970s and into the 1980s, PBI was instrumental to space flight, seeing application on Apollo, Skylab, and numerous space shuttle missions. Applications ran the gamut from the intended applications in astronaut flight suits and clothing, to webbing, tethers, and other gear that demanded durability and extreme thermal tolerance.
Advertisement
Today, you’ll find PBI fabric used in all sorts of applications, including firefighting and motorsports (where it’s used in race suits).
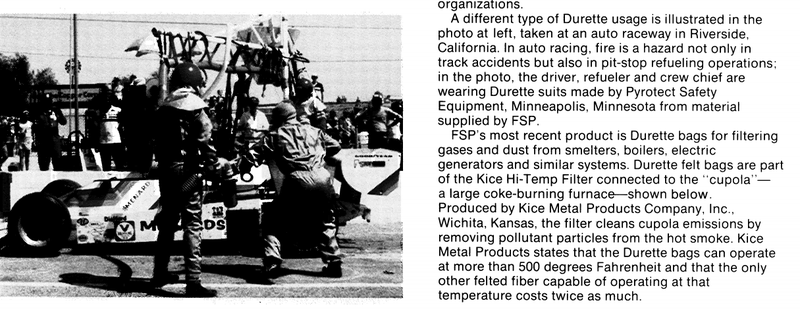
Advertisement
There were a number of other flame-retardant materials that came into play after the Apollo fire, including a fabric called Durette, which was used for astronaut clothing due to the fact that it did not “burn or produce noxious fumes” according to NASA. Developed by a St. Louis-based company called Monsanto under contract with Johnson Space Center, the fabric’s rights were eventually sold to Fire Safe Products, who—per the image above—sold the material to “Pyrotect Safety Equipment,” who made some safety suits for a race car.
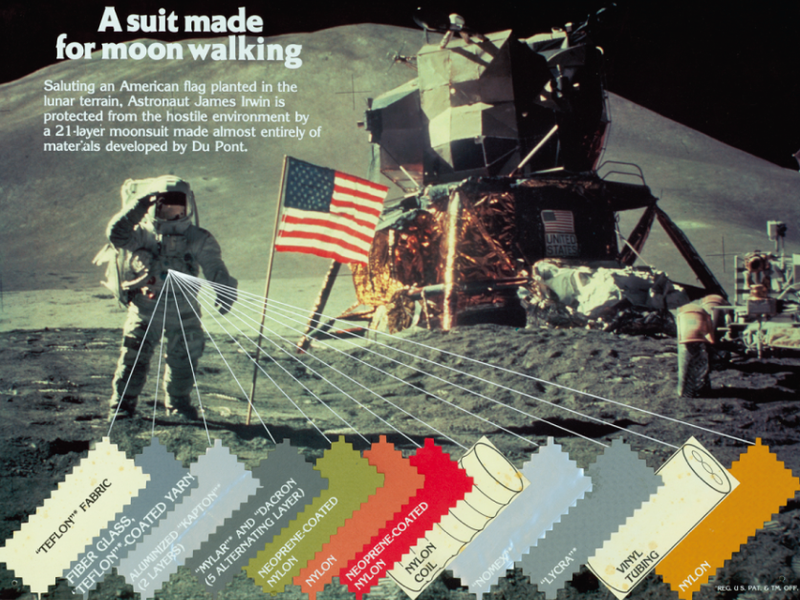
Advertisement
Incidentally, the most common fabric used for race suits today—and the one required for Formula One by the FIA—isn’t actually PBI or Durette, but rather something called Nomex, a Du Pont invention that, Du Pont says, was among the 21 layers found in the space suits used during the Apollo 11 mission.
A Special Coating for the Apollo Heat Shield Used as Fire Protection on Airplanes
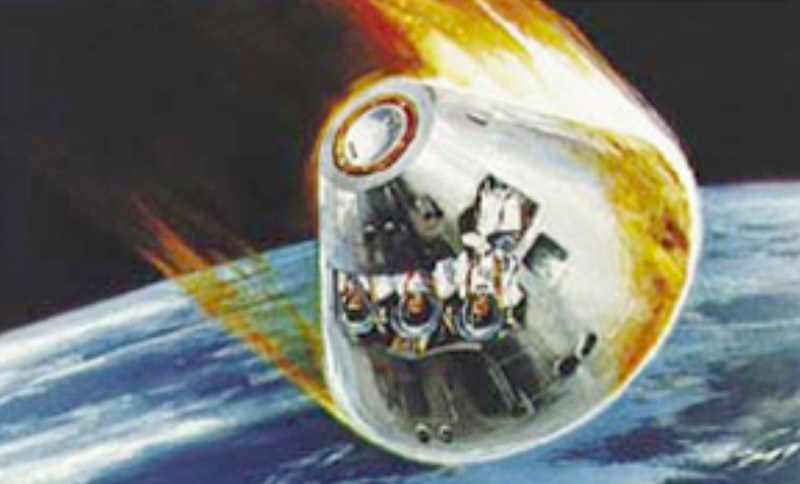
Advertisement
The Apollo 1 tragedy apparently led to some serious changes at NASA, and lots of testing then took place to make sure the machines were thermally safe. Here’s some of that testing involving ensuring that the orbiter’s heat shield kept the vehicle’s interior temperatures down, per NASA’s website:
After the spacecraft achieved an altitude of 10,000 miles, its engines drove it back down into the Earth’s atmosphere at an unprecedented speed of approximately 25,000 miles per hour. During reentry, temperatures on the orbiter’s heat shield reached 5,000 °F, more than half the surface temperature of the Sun. The heat shield charred as expected, but the spacecraft’s inside cabin remained a comfortable 70 °F. A milestone had been passed, Low wrote, making way for man to go to the Moon.
Advertisement
The heat shield was built by Avco Corporation, and was coated with a special material that was designed to dissipate energy and to intentionally char to “form a protective coating which blocked heat penetration beyond the outer surface,” NASA says. The agency writes about how this coating was “spun off” to be used for in industry. Particularly, on aircraft:
Avco Corporation subsequently entered into a contract with Ames Research Center to develop spinoff applications of the heat shield in the arena of fire protection, specifically for the development of fire-retardant paints and foams for aircraft. This experience led to the production of Chartek 59, manufactured by Avco Specialty Materials (a subsidiary of Avco Corporation eventually acquired by Textron, Inc.) and marketed as the world’s first intumescent epoxy material. As an intumescent coating, Chartek 59 expanded in volume when exposed to heat or flames and acted as an insulating barrier. It also retained its space-age ablative properties and dissipated heat through burn-off.
Advertisement
The Dustbuster: A Classic Car-Cleaning Vacuum
Advertisement
Okay, so this one might not be directly transportation-related, but handheld cordless vacuums are arguably at their best when they’re used to clean cars. And possibly the most successful one of all time was the Dustbuster, sold by Black and Decker starting in 1979.
Per NASA, this Floorboard Lingering Cheeto-sucking contraption actually came out of the Apollo Program. Well, sort of. From NASA’s website:
Portable self-contained drill capable of extracting core samples as much as 10 feet below the surface was needed for the astronauts. Black & Decker used a specially developed computer program to optimize the design of the drill’s motor and insure minimal power consumption. Refinement of the original technology led to the development of a cordless miniature vacuum cleaner called the Dustbuster.
Advertisement
Surely You’re All Aware of the Goodyear Blimp
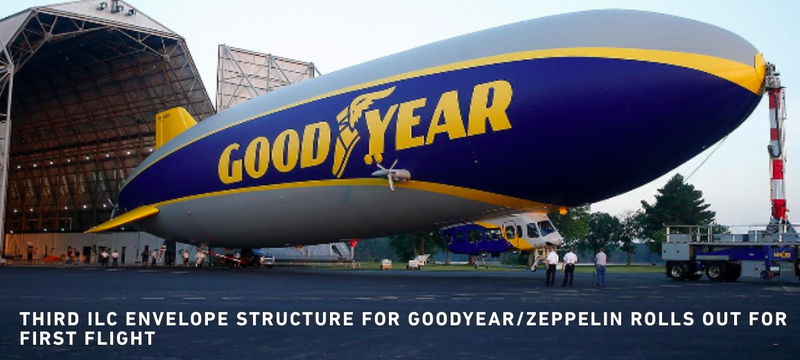
Advertisement
The company that built the space suit for the astronauts and continues to do so to this day (and the one that apparently also made bras), ILC Dover, is the same company that also builds lighter than air vehicles, including components found in the Goodyear blimp.
From NASA:
Through its work with space suit designing, testing, and manufacturing, ILC Dover developed skills and processes unique to industry. It has harnessed this space know-how on numerous occasions and has developed several spinoff products. The work ranges from therapeutic suits to safe, efficient pharmaceutical manufacturing; to new, simple-to-use, life-saving gas and chemical masks; and to lighter-than-air (LTA) vehicles.
Advertisement
There’s a Lot More That Came out of Apollo
These were just a couple of examples that NASA sent me, but there are plenty more. Paul Ceruzzi, a curator emeritus at the National Air and Space Museum, told me in a phone interview that a number of innovations from Apollo likely trickled down into the auto industry.
Advertisement
The main one, he mentioned, was the fact that Apollo was a very early example of “digital control taking the place of mechanical control” of a combustion engine—something that has since happened en masse to the automobile industry. “Prior to Apollo, the rockets were controlled by mechanical devices,” he told me.
That Apollo Guidance Computer really was ahead of its time, especially with its integrated display and keyboard (called DSKY or“diskey”). Apollo’s guidance computers set the table for computer-control in automobiles, according to MIT:
“The Apollo Guidance Computers were early examples of what we would today call ‘embedded’ computers — which now appear in everything from iPhones to automobiles,” said MIT Professor David Mindell, author of “Digital Apollo” which explores how human pilots and automated systems worked together to achieve the successful lunar landing. “The MIT machines showed the world that computers, previously known as refrigerator-sized cabinets, could be made small and reliable enough for even the most demanding, and life-critical applications.”
Advertisement
Ceruzzi also mentioned advancements in accelerometers that were likely adopted in cars, and said progression of precision of manufacturing and high temperature resistant materials have likely filtered down to the auto industry, as well.
One thing he did make clear was just how different designing a car is that designing a spacecraft. The ramifications of a failure are extremely different, and also, there’s cost. “Apollo, cost was not the issue,” he said.
“It was quality. So that doesn’t translate at all.”
It’s a fair point to make.
Still, even if lots of the parts designed for Apollo would have broken the bank for an auto manufacturer, it’s clear that the research that went into the mission has yielded great benefits to humankind, and to the transportation industry. You can read more about NASA’s transportation-related spinoffs on its website.
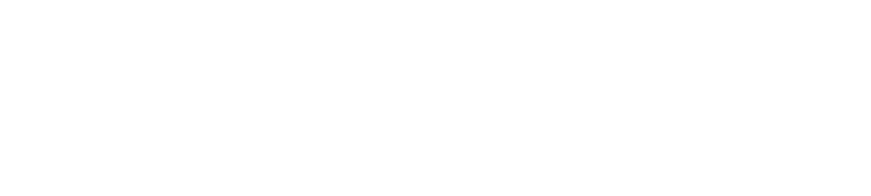