
Rust removal has been my specialty ever since I moved to Michigan in 2013 (out of necessity). My normal method for getting rust off my cars is simply to lightly blow on their chassis or to drive over small bumps. But last week I tried a more effective method of rust removal: electrolysis. And it is glorious.
Electrolysis is a well-known rust removal technique in wrenching circles, but I’d never tried it myself until last week. Right now I’m trying to fix my 1979 Jeep Cherokee Golden Eagle before Detroit’s harsh winter settles in, and one of the main hurdles is the frame.
To be sure, the engine still isn’t running, but I bet I’ll be able to “smoke” that thing up in the next few days. From there, I’ll need to install the grille and front bumper. I just finished polishing the grille, and with a few screws, that should pop right onto the Jeep’s face, covering up the surface that once acted as the SJ SUV’s face on previous generations. The bumper, though, won’t be that simple, since the dealership that sold the Jeep cut off the frame horns to fit a winch bumper meant for pre-1979 SJs.
This means that to install the bumper I bought from a chicken and bee-infested North Carolina junkyard, I’ll need to weld on some frame horns. The issue is that the only frame horns I have are ones I sliced off of a Jeep Grand Wagoneer in a Pontiac, Michigan, junkyard. It should be no surprise that they are rusty. A wiser man would have just walked away, but I was desperate:

I wasn’t keen on the idea of trying to grind the rust off of these with an angle grinder, since the parts feature bends and holes that would have made it a bit time consuming. So the solution was…well, a solution.

Specifically, it was a solution of water and washing soda — a combination that would act as the electrolyte in my electrolysis rust-removal experiment.
I poured the mixture into a plastic bucket, suspended my rusty frame horns (clamped together with Vise Grips) in the solution with a coat hanger and dropped a steel U-Bolt into the liquid, as well.
I then hooked the negative clamp of a jumper wire to the coat hanger, and the positive clamp to the U-bolt, with the two jumper wires being connected to a car battery on the other end. The positive U-bolt was to act as my sacrificial anode, quickly rusting, as the cathode — my frame horns — shed its rust.

Flip through these Instagram videos to see the experiment in action:
It took only a couple of hours for my frame horns, hooked to the negative post of a 12-volt battery that was being trickle-charged, to shed all of its brown. Behold:

I did scrub the parts for a couple of minutes to knock off any remaining brown rust. This was easy and required little force, as the rust was barely clinging to the parts.
This little experiment was the easiest rust removal technique I could have expected. Pour water with washing soda into a bucket, submerge rusty part, submerge sacrificial piece of steel, hook positive to sacrificial anode, hook negative to part. Voilà. Total setup was five minutes max, and total rust removal time was a few hours of mostly waiting.
The actual science behind electrolysis is fairly complex. As I understand it, the washing soda, or sodium carbonate, introduces ions that act as charge carriers, allowing for current flow. I haven’t found a ton of authoritative literature on this, but I did find this random, seemingly scientific paper by someone named Sandra Goria. She describes the role of the carbonate washing soda, writing:
Thus, when including sodium carbonate into the solution, the sodium and carbonate dissociate, hence, sodium becomes the cation (Na2 +) and carbonate becoming the anion (CO3 2-). The resistance is lowered due to the introduction of the movement of ions which allow the current to flow easily. This is due to the fact that ions are charge carriers in the solution.
As for how exactly the electrochemical process of rusting can run in reverse, the paper goes into the oxidation-reduction reactions involved, writing:

The Institute of Nautical Archeology at Texas A&M discusses electrolysis, also called Electrolytic reduction, a bit on its website.
The essence of the technique involves setting up an electrolytic cell with the artifact to be cleaned as the cathode. An electrolytic cell consists of a compartment or vat with two electrodes, the anode and the cathode, and contains a suitable electricity-conducting solution called the electrolyte. An electric current from an external direct current (DC) power supply is applied to cause oxidation and reduction.
The text continues, mentioning the reduction reaction at the cathode (which, again, is the rusty part):
The anode is the positive terminal of the electrolytic cell, to which electrons, negatively charged ions, or colloidal particles, travel when an electric current is passed through the cell. Oxidation occurs at the anode and oxygen is evolved. The cathode is the negative terminal of an electrolytic cell, to which positively charged metallic ions travel. At the cathode, reduction takes place and hydrogen is evolved. In the reduction process, some of the positively charged metal ions in the compounds on the surface of the artifact are reduced to a metallic state in situ. In addition, chlorides and other anions are drawn from the specimen and migrate toward the positively charged anode by electrolytic attraction.
Obviously, flaky rust that has separated and flaked off the part will be lost, but other rust on the part can be saved. It’s also worth mentioning that there are some safety precautions that you need to take when running this experiment, as dangerous and potentially flammable gases can form.
Hit up YouTube if you want to see more electrolysis rust removal in action. Behold:
While you’re doing that, I’ll be trying to fire up the AMC 360 in this thing:

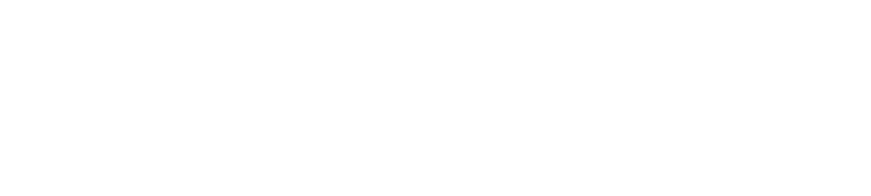