
The 2021 Ford F-150 has a feature called “Onboard Scales,” which uses the taillights to help make sure you don’t overload the truck beyond its payload capacity. Here’s how this works.
I’m always impressed when automotive software engineers use already-existing hardware to develop useful new features. Ford’s Trail Control (off-road cruise control) and Trail Turn Assist (a feature that brakes the rear inside wheel to allow for a tighter turn) are two great examples that take advantage of drive-by-wire and the vehicle’s highly capable ABS system.
Now there’s Onboard Scales. My taillight-fetishizing coworker Jason Torchinsky pretty much had a stroke when he saw this feature, as you could probably tell by his article. While that story did a great job contextualizing what this moment means in the grant scheme of taillight history, it didn’t really describe how the system works. Neither did our introductory article in April.
Seeing as Jason’s taillight story is the most-clicked-upon story on Jalopnik right now, and seeing as I just had a chance to test out Onboard Scales at a Ford press event yesterday, I thought I’d write a bit about how the tech works. It’s not going to be one of my patented deep dives, but it’ll be a nice, light overview. Here we go.
The video above shows Onboard Scales (which will tell the driver via either the four bars in each taillight, the infotainment screen, or a phone app how close the vehicle is loaded weight is to max payload) and Smart Hitch (which uses the bars to help the driver determine when the vehicle has the appropriate trailer tongue weight) in action.

With Onboard Scales, you want the taillights to remain below four bars (the lights will blink once you hit the payload limit) while with the Smart Hitch feature, you want the center two bars to be lit (the lower bar will blink if the tongue weight is too low, the upper if it’s too high — see below).

On the infotainment screen, the Onboard Scales function will give you a horizontal line that rises and falls relative to a red and green bar as you throw weight (or passengers) into the vehicle. The green represents load conditions within payload limits, and is broken into four quartiles that each correspond to an LED in each taillamp. When the horizontal bar reaches the red zone, the vehicle is overloaded.
Ford has some guidance bars to make sure you don’t forget to account for passengers (you can input passenger weight into the system).

Another display mode in the Onboard Scales software, shown below, helps drivers understand how much weight they’ve added to their truck. Rather than having a bar that adjusts relative to the max payload limit, this view allows the driver to set the scale to zero to understand rough weights of additional cargo.
Note that I say “rough,” as the system is only accurate to within 200 pounds. That’s quite a range. “At the vehicle level it’s plus or minus 200 pounds,” F-150 chassis controls engineer Jorge Rivas told me. “That covers the loading range and all the different conditions,” he continued, saying the truck “could be a little bit overloaded at that point [when all four lights are on]” given the 200 pound confidence interval.
“Customers still have to be careful and responsible for the overall loading,” he told me, noting also that the payload limit does include a full tank of gas. (I don’t know exactly how Ford accounted for that. The way I understood it, filling up your truck will never bring you beyond the red line. I don’t know if the truck reads the fuel tank status to adjust the limits, or if there’s some kind of big large safety factor (roughly 150 pounds in a 23 or 26 gallon tank) built in).

As for the Smart Hitch function, that shows a horizontal bar relative to a green bar that floats between two small red bars (see below). The bottom red bar represents a condition where the tongue weight is too low (below 10 percent of trailer weight, which the user inputs into the system manually), and the top bar representing a tongue weight that’s too high (above 15 percent of trailer weight).
Proper tongue weight is important, as it can affect how the truck and trailer behave (high tongue weight can cause the tow vehicle to understeer, and it can negatively affect braking performance; a low tongue weight can cause uncontrollable trailer sway). Payload is important for many of the same reasons.

So how does all of this work? What exactly is feeding the taillights and the infotainment screen?
Ford’s system uses ride height sensors, which are fairly standard parts that you normally find in vehicles equipped with air suspension (the ride height sensors tell the system to stop filling air springs when a desired height has been reached). The F-150 doesn’t have air suspension, but it does have adaptive damping, which uses ride height sensors to monitor certain vehicle handling characteristics like body roll, and to get an idea of road conditions. The system uses this is as an input to adjust damper settings.
Here, allow Ford to walk you through how it uses ride height sensor input to adjust the suspension:
The all-new 2021 F-150 offers available continuously controlled damping for enhanced ride and handling characteristics, especially when towing or hauling heavy loads. A computer within the F-150 analyzes multiple signals collected from high-resolution sensors – adjusting vehicle response to each situation by controlling valves in the shocks.
Damping force is used to control unwanted motions such as bounce, pitch and roll reducing the severity the truck – and its passengers – will feel from traveling through the pothole. When the edge of a pothole is detected, the dampers firm up, preventing the tires from dropping as deep into the hole. Tuning can be adjusted by selecting any of the available drive modes.
You may recall that the Ford Raptor’s ride height sensors allow the truck to detect when the vehicle is in the air, firming up the dampers to prevent the suspension from bottoming-out upon landing. Here’s a quote from my review (where I detail what it was like jumping the 2019 Ford Raptor):
Plus, thanks to the rotary ride height sensor on the control arm (shown above), the truck can tell when it’s airborne, as both wheels would then be in full rebound. When it does notice the car is flying through the air, the system adjusts shocks to their stiffest settings—which Ford says can result in up to 400 additional pounds of damping force—to yield a smooth and bottom-out-free landing.

Ride height sensors are funny looking things. One end of a skinny pushrod hooks to a bracket hard-mounted to the vehicle’s chassis, while the other end attaches to a lever arm that’s part of a rotary sensor (I’ll guess it’s a potentiometer, of sorts) mounted to a suspension component that moves anytime the wheel travels up and down.
In the case of the 2021 Ford F-150’s rear suspension, the ride height sensor is hooked to the frame on one end and to the top of the leaf spring pack on the other (specifically, it fastens to the leaf spring center pins, whose job is to bolt the leafs in a leaf spring pack together, and to locate that spring pack on the axle spring perch so that there’s no relative motion).

This is a little beyond the scope of this article, but I want you to know exactly where this ride height sensor is mounted, so take a look at this image of the rear suspension without the ride height sensor, courtesy of one of Dan Edmunds’ always-excellent suspension deep-dives. Though I haven’t looked at the leaf pack closely, it’s safe to say the two bolts where the sensor mounts are the center pins that locate the spring to the axle by passing through the main leaf, through the helper spring, through the spacer, and poking down into two holes in the spring perch welded to the axle tube (I’ve added some arrows to Dan’s image):

Notice how long the rear sensor’s lever arm is (two images above); I’m assuming this has to do with the tremendous suspension travel of that rear suspension, particularly at the point of measurement there at the center of the leaf pack. I’m also assuming this accounts for a leaf spring’s motion in the X-direction (the center of a leaf spring doesn’t just travel perfectly up and down, it also moves longitudinally).
As I understand it, the truck above with the rear rotary sensor is not equipped with Ford’s semi-active damping system, so the sensor is an add-on component there specifically for the Onboard Scales and Smart Hitch features. For vehicles that do have Continuously Controlled Damping (CCD), the sensor that provides rear ride height data is actually linear and built into the damper:

The front suspension’s rotary sensor doesn’t require as large a lever as the rear sensor on trucks without CCD, because there’s a nice pivot arm (the upper control arm) whose small displacement inboard corresponds to a large wheel displacement farther outboard on the arm where the steering knuckle mounts.
Notice how far inboard on the control arm the sensor bolts up; you’ll see that the other side of the sensor is hooked to the frame just ahead of the shock/spring tower:

To get from the vertical displacement measurements (which Ford says are accurate to less than a tenth of an inch) that the ride height sensors generate to the weight of the load in the truck, Ford engineers are essentially using Hooke’s law: Force = spring constant * displacement.
Ford is well aware of what the spring constants are at the front and rear of the truck, since these are critical parameters needed to tune a suspension. With displacement readings coming from the sensors, Ford can then calculate the Force being exerted onto the truck in pounds. Note that, for coil springs, this k-value (the spring constant) is a single number, though for leaf springs, things are a little more complicated, as a suspension engineer told me over email:
The k factor of the coil spring is very linear and reliable. For the leaf it’s a non linear force/displacement curve that changes over time since leafs wear and smooth out over their life. Today’s leafs also have inter-lead coatings to reduce friction. Finally, there are new one piece composite leaf springs on the Volvo SPA, latest Ford Transit, etc. that completely eliminate the issue and are basically equivalent to coil springs for hysteresis. If Ford puts this system into the Transit for Europe it will be much more accurate. There is an upcoming vehicle payload detection regulation in the EU so many OEMs are asking about payload monitoring.
So with Ford understanding its k-values (relationship between load and displacement), and having displacement sensors, backing out how much load is in the truck should be easy, right? Maybe for Ford engineers, but to the layperson, it’s not.
There are many, many different F-150 configurations with different spring rates (depending upon things like wheelbase, cab configuration, trim package), different curb weights (depending upon how they’re equipped — a highly-contented Limited trim is going to have a higher curb weight, and thus a lower max payload), and differences in bushings and shackle geometry.
The differences in geometry mean “height sensors are not always in exactly the same location,” Rivas told me at the press event yesterday, resulting in “each vehicle [being] individually calibrated, so we know we have a very accurate system.”
“It’s a single software,” he continued, telling me the system uses the controller normally used for the Continuously Controlled Damping system. “We have different calibrations for each variant…it was upwards of 40 cals, and we’re working to improve that,” he told me, going on to say that the calibration is tied to each vehicle’s VIN.
In addition to vehicle complexity, another important consideration when developing the system has to do with hysteresis. You may have seen this curve before describing the concept of hysteresis:

Essentially, what it describes is how, when you load up a system, you may get a certain displacement, but when you remove that same load from the system, it won’t necessarily return to its starting point due to losses from friction. So you can have an instance where the exact same weight in a truck bed gives you two different displacement readings from the ride height sensors (illustrated by A and B above, though the curve above isn’t representative of the system, it’s just there to illustrate a concept). So how do you come up with a good correlation between ride height and load? Well, you have to consider time.
“When you compress a suspension and release it again, it won’t always go back to the same position, so we account for that,” Rivas told me. “We’re looking live at that motion to understand what we think is the actual weight on the truck, not just based on the current position, but the history of the position.”
My suspension engineer contact provided a little more insight, saying:
That’s an interesting idea from Ford. I would assume that they are recording or tracking the vehicle height sensor position during large payload changes when the truck is at rest. They could then see the cloud of points around certain heights and have some type of compensation over time if they see a trend.
I heard that they can only detect a weight delta of around 200 lbs. So the friction of the leaf springs are definitely a large percentage of this uncertainty. Obviously coil springs are better for hysteresis (old ride and handling bounce tests – push down hard once on the fender or bumper and see where the height is pre and post the push – I did gave an error on 0.5” max. between repetitive pushes). For leaf springs the internal friction is the driving factor for hysteresis. For coil spring suspensions it’s actually the suspension bushing hysteresis that has the largest effect. For air springs it’s more complicated since you then have a combination of errors (airbag hysteresis, bushings, air valves, etc.)
Finally, there is the error of the actual rotary height level sensor, which is probably at least half of the current F150 error. ZF just showed our integrated smart ball joint at the IAA in Munich which has the potential to cut down the 200 lbs. error to 100 lbs., at a minimum.
In the end I am impressed that Ford developed this application for their customers and this is just the first step into many more smart suspension applications that will be coming to the market in the next 5-10 yrs. as suspensions add integral sensors into previous “dumb parts” to aid Autonomous driving.
What about the location of the weight; does that matter? Isn’t that going to change which sensors read what? Well, for Ford’s system, the location of the weight isn’t really relevant, since Onboard Scales just gives an overall truck payload figure. “We have sensors in each corner, and that helps us identify where the weight is loaded…the only information we provide is overall load. Rather than doing it individually per axle, we just add up the overall number,” Rivas said.
Onboard scales with Smart Hitch will cost $650 and will add ride height sensors and a computer. If you want Continuously Controlled Damping (which replaces rear rotary sensors for linear ones), that adds $695.
The system is obviously imperfect. Ford has to account for so many different vehicle variations, the Smart Hitch system has to make assumptions about the user’s hitch geometry, there are inaccuracies in the sensors, there are calculations that need to be made about hysteresis, and on and on. In the end, the system is only accurate to within 200 pounds, and while that may not be great if you’re using your truck to measure how many pounds of grain you’re carrying to sell at the local elevator, it’s good enough to give users peace-of-mind, and keep them from vastly overloading their vehicles without knowing. And that has value.
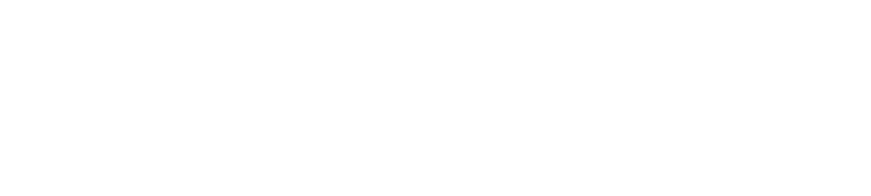