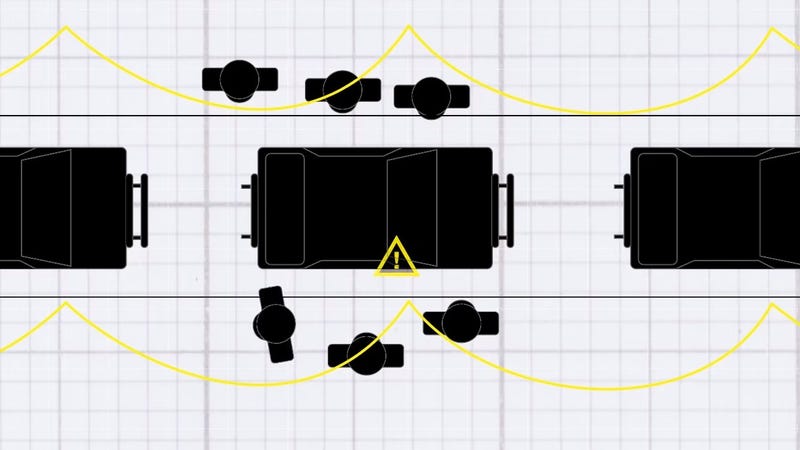
Much praise has been heaped upon Henry Ford and his implementation of the assembly line as it relates to assembling complete automobiles, even though credit for the invention really belongs to Ransom E. Olds, and he doesn’t get enough for it. Similarly, laudatory language is rarely thrust in Taiichi Ohno’s direction, even though he was instrumental in revolutionizing Toyota’s manufacturing systems, and manufacturing systems all over the world. For a brief understanding of Toyota’s plan, and how it has been changing the world of manufacturing for the last 60 years, check out the video below from Bloomberg.
Those systems would go on to become the standard of the world, which are still largely employed today. Lean manufacturing, just-in-time inventory, kanban, and kaizen are all part of that process. By producing the individual components in smaller batches, and fixing problems as they cropped up, Toyota was able to continually improve its process structures to build cars faster, improve company efficiencies, and reduce errors and re-work.
Other companies have looked to Toyota for assistance in revamping their own manufacturing facilities to make use of these kanban and kaizen philosophies. Porsche partnered with Toyota in 1990 for just that reason, and it might have just saved their asses. But it’s not just limited to automotive companies, as nearly every company from Boeing to Nestlé and even the Mayo Clinic have implemented these ideals to smooth out operations.
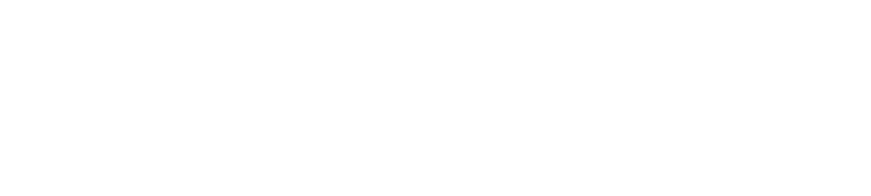